To troubleshoot a Liftmaster RSL12UL, check power supply connections and inspect the control board for any error codes. Ensure safety sensors are aligned and clean.
The Liftmaster RSL12UL is a robust gate operator used in both residential and commercial settings. Proper troubleshooting ensures its optimal performance and longevity. Common issues include power supply problems, sensor misalignment, and control board errors. Start by confirming that all power connections are secure and intact.
Inspect the control board for any error codes that might indicate specific issues. Ensure safety sensors are aligned and free of debris. Regular maintenance and prompt troubleshooting can prevent major breakdowns and extend the lifespan of your Liftmaster RSL12UL gate operator.
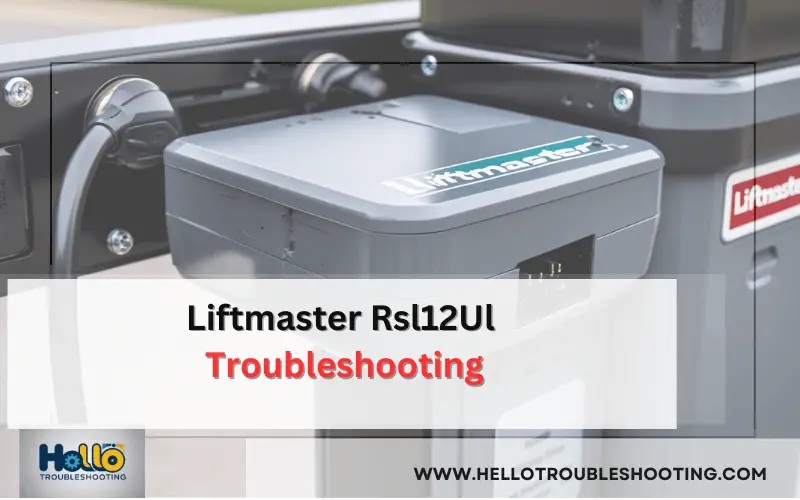
Initial Checks
Experiencing issues with your Liftmaster Rsl12Ul? Start with initial checks. These simple steps can solve most problems quickly.
Power Supply Inspection
First, inspect the power supply. Ensure the unit is plugged in properly. Check for any visible damage to the power cord. Use a multimeter to verify the voltage. The power outlet must deliver the correct voltage. If not, try another outlet. Ensure no power interruptions.
Remote Control Battery
Next, check the remote control battery. A weak battery often causes issues. Open the remote control’s battery compartment. Replace the old batteries with new ones. Ensure the batteries are inserted correctly. Test the remote to see if it works. If the remote still doesn’t work, consider reprogramming it.
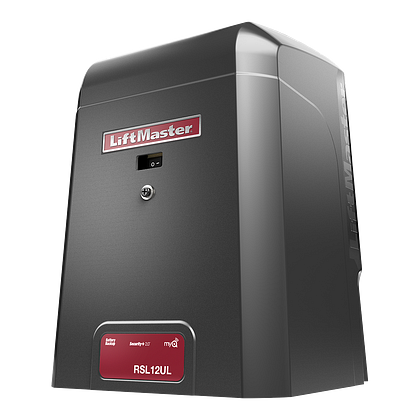
Credit: www.liftmaster.com
Gate Movement Problems
Experiencing issues with your Liftmaster RSL12UL gate movement can be frustrating. These problems can stem from various causes. This guide will help you troubleshoot and resolve common gate movement problems.
Obstruction Detection
The Liftmaster RSL12UL gate has a built-in obstruction detection feature. This feature prevents the gate from closing on objects or people. An obstructed gate will stop or reverse direction.
- Check for physical obstructions like rocks, debris, or plants.
- Inspect the sensors for dirt or damage. Clean them if needed.
- Ensure the gate path is clear and free of obstacles.
If the gate still doesn’t move, the sensors might need recalibration. Follow the manual for recalibration instructions.
Motor Malfunctions
Motor problems can also cause gate movement issues. A malfunctioning motor might result in a gate that won’t open or close.
- Listen for unusual noises from the motor. Grinding sounds can indicate damage.
- Check the motor’s power supply. Ensure it is connected and receiving power.
- Inspect the wiring for any visible damage or loose connections.
If the motor appears fine, but the gate still doesn’t move, consider performing a system reset. A reset can sometimes resolve minor glitches.
Here is a quick troubleshooting table:
Problem | Possible Cause | Solution |
---|---|---|
Gate not moving | Obstruction detected | Clear the path, check sensors |
Gate stops midway | Sensor issue | Clean or recalibrate sensors |
Unusual motor noise | Motor damage | Inspect and repair motor |
By following these steps, you can troubleshoot most gate movement problems. Regular maintenance can also prevent many issues from occurring.
Sensor Issues
Liftmaster Rsl12Ul sensors are crucial for safe operation. Sometimes, they face issues. These sensors can stop the gate from moving. Let’s explore common problems like alignment and dirty sensors.
Alignment Problems
Alignment issues are common in gate sensors. The sensors might not point correctly. This misalignment can stop the gate from closing.
- Check if the sensors are directly facing each other.
- Adjust them if they are not aligned.
- Use a level tool to ensure they are straight.
- Tighten the screws after aligning the sensors.
A small misalignment can cause big problems. Always check the alignment first.
Cleaning Sensors
Dirt and debris can block the sensors. This blockage can prevent the gate from working.
Step | Description |
---|---|
1 | Turn off the power to the gate. |
2 | Gently wipe the sensor lenses with a soft cloth. |
3 | Remove any spider webs or dirt around the sensors. |
4 | Turn the power back on and test the gate. |
Cleaning the sensors regularly can prevent many issues. It ensures the gate works smoothly.

Credit: www.reddit.com
Control Board Errors
The Liftmaster Rsl12Ul gate opener is a reliable piece of equipment. However, it can face issues related to the control board errors. Understanding these errors is crucial for smooth operation. In this section, we’ll explore error code interpretation and resetting the control board.
Error Code Interpretation
The control board displays error codes for diagnosing problems. Below is a table of common error codes and their meanings:
Error Code | Description |
---|---|
E1 | Power Failure |
E2 | Motor Overload |
E3 | Sensor Failure |
E4 | Obstruction Detected |
If you see an error code, refer to this table. It helps identify the issue quickly. For example, E1 means a power failure. You should check the power supply.
Resetting The Control Board
Sometimes, resetting the control board can solve the problem. Follow these steps to reset the Liftmaster Rsl12Ul control board:
- Turn off the power supply to the gate opener.
- Wait for at least 30 seconds.
- Turn the power supply back on.
- Check if the error code has disappeared.
If the error persists, you might need further troubleshooting. Consult the manual or contact customer support for additional help.
Remote Control Troubles
Experiencing issues with your Liftmaster Rsl12Ul remote control? This guide will help you resolve common problems. We will cover reprogramming the remote and understanding range limitations.
Reprogramming Remote
If your remote isn’t working, try reprogramming it. Follow these simple steps:
- Locate the learn button on the motor unit.
- Press and release the learn button. The indicator light will glow.
- Within 30 seconds, press and hold the button on the remote.
- Release the button when the motor unit light blinks. This confirms programming.
If the remote doesn’t work, repeat the steps. Ensure the remote battery is fresh.
Range Limitations
The remote control has a limited range. Common issues include:
- Interference from electronic devices.
- Obstacles like walls and large objects.
- Weak battery in the remote.
To improve the range, try these tips:
Issue | Solution |
---|---|
Interference | Move electronic devices away from the motor unit. |
Obstacles | Ensure a clear path between the remote and the unit. |
Weak Battery | Replace the battery with a fresh one. |
If issues persist, check the antenna on the motor unit. Ensure it’s properly extended.
Maintenance Tips
Regular maintenance of your Liftmaster Rsl12Ul ensures smooth operation and long life. Follow these tips to keep your gate opener functioning perfectly.
Lubrication Of Moving Parts
Lubrication is crucial for the smooth operation of your gate opener. Ensure you lubricate all moving parts regularly.
- Use a high-quality lubricant.
- Focus on hinges, rollers, and chains.
- Avoid over-lubricating; a small amount is enough.
Lubricate every six months for best results. This reduces wear and tear.
Regular Inspection Schedule
Inspect your Liftmaster Rsl12Ul regularly to catch issues early. Use this checklist:
Inspection Item | Frequency |
---|---|
Check for loose bolts | Monthly |
Inspect electrical connections | Quarterly |
Examine gate alignment | Monthly |
Test safety features | Monthly |
Regular inspections ensure your gate opener operates safely and efficiently.
When To Seek Professional Help
Troubleshooting a Liftmaster Rsl12Ul gate opener can be challenging. Sometimes, issues are too complex to handle alone. Knowing when to seek professional help is crucial. This section will guide you through identifying such situations and finding the right technician.
Identifying Complex Issues
Some issues are beyond simple fixes. Here are a few signs you need professional help:
- Unusual Noises: Grinding, squeaking, or clanking sounds.
- Intermittent Operation: Gate opens and closes unpredictably.
- Electrical Problems: Blown fuses or persistent power issues.
- Mechanical Failures: Broken parts or misaligned components.
These issues often require specialized tools and expertise. Attempting to fix them yourself might make things worse.
Finding A Qualified Technician
Finding the right technician ensures your gate opener gets fixed correctly. Consider these steps:
- Check Certifications: Look for Liftmaster-certified technicians.
- Read Reviews: Search for reviews from previous customers.
- Ask for Recommendations: Speak to friends or neighbors.
- Compare Quotes: Get multiple quotes to find the best deal.
A qualified technician will have the necessary skills and experience. They can diagnose and repair complex issues efficiently.
Frequently Asked Questions
How Do I Reset My Liftmaster Rsl12ul?
To reset, turn off the power, wait 10 seconds, then turn it back on.
Why Is My Liftmaster Rsl12ul Not Working?
Check the power supply, control board, and limit switches for issues.
What Causes Liftmaster Rsl12ul Gate To Stop?
Gate may stop due to obstruction, power failure, or motor issue.
How To Troubleshoot Liftmaster Rsl12ul Error Codes?
Refer to the manual for specific error codes and troubleshooting steps.
Can Liftmaster Rsl12ul Be Repaired At Home?
Minor issues can be fixed at home, but complex repairs need professional help.
Conclusion
Troubleshooting the Liftmaster RSL12UL can be straightforward with the right steps. Regular maintenance ensures optimal performance. Always consult the manual for specific issues. Seek professional help if problems persist. Ensuring your gate opener works efficiently guarantees safety and convenience. Stay proactive and keep your Liftmaster in top shape.