Ice O Matic ice machines are reliable, but problems can occur. Understanding common issues helps maintain performance.
Ice machines are essential for many businesses. When they fail, it disrupts operations. Knowing how to troubleshoot Ice O Matic ice machines can save time and money. This guide will help you identify and fix common problems. Learn how to spot issues early and keep your machine running smoothly.
Whether it’s ice production problems or unusual noises, we’ve got you covered. Keep reading to ensure your Ice O Matic ice machine works efficiently.
Common Issues
Ice-O-Matic ice machines are reliable, but issues can arise. Knowing common problems helps with quick fixes. Here are some frequent issues and how to address them.
No Ice Production
When the Ice-O-Matic ice machine stops producing ice, several factors might be at play. First, check the power supply. Ensure the machine is plugged in and the circuit breaker is not tripped.
Next, inspect the water supply. The water line should be connected and the valve open. A clogged water filter can also halt ice production. Replace the filter if necessary.
Another cause could be the thermostat settings. Ensure the thermostat is set correctly. If the issue persists, there might be a problem with the internal components. A professional technician can help.
Slow Ice Production
Slow ice production can be frustrating. Start by examining the ambient temperature. High room temperatures can slow ice production. Keeping the area cool helps.
Check the condenser coils. Dirty coils reduce efficiency. Clean them regularly with a soft brush or vacuum.
Also, inspect the water supply. Low water pressure or a partially closed valve can affect ice production. Ensure the valve is fully open and the pressure is adequate.
Lastly, ensure the machine is level. An uneven surface can disrupt ice production. Adjust the machine’s feet if needed.
Initial Checks
When your Ice O Matic ice machine stops working, performing initial checks is crucial. These simple steps can often identify and resolve common issues. By addressing these basics, you can save time and avoid unnecessary service calls.
Power Supply
First, verify that your ice machine has power. Check the power cord and ensure it is properly plugged into the outlet. If the machine is not turning on, try plugging another appliance into the same outlet to see if it works. If the outlet is faulty, you may need to reset the circuit breaker.
Ensure the power switch on the ice machine is in the “On” position. Sometimes, the switch can be accidentally turned off. Also, inspect the power cord for any visible damage. If you see any frayed wires or other issues, the cord might need replacing.
Water Supply
Next, check the water supply. Make sure the water line is connected and the water valve is open. If the valve is closed, the machine will not get any water to make ice. Inspect the water line for kinks or bends that might restrict water flow.
Ensure the water filter is clean and not clogged. A dirty filter can block water from entering the machine. If it has been a while since you last changed the filter, it might be time to replace it. Regular maintenance of the water filter can prevent many issues.
Checklist | Action |
---|---|
Power Cord | Ensure it is plugged in and undamaged |
Power Switch | Verify it is in the “On” position |
Outlet | Test with another appliance |
Water Line | Check for connection and kinks |
Water Valve | Ensure it is open |
Water Filter | Inspect and clean or replace if needed |
Performing these initial checks can often resolve common problems with your Ice O Matic ice machine. By ensuring the power and water supplies are working correctly, you can help your machine run smoothly and efficiently.
Cleaning Procedures
Regular cleaning of your Ice O Matic ice machine ensures optimal performance. It prevents build-up and maintains ice quality. Follow these cleaning procedures to keep your machine running smoothly.
Descaling The Machine
Descaling removes mineral deposits that accumulate over time. These deposits can affect the taste and clarity of your ice.
- Turn off the ice machine and disconnect the power supply.
- Remove the ice bin and discard any ice.
- Mix a descaling solution according to the manufacturer’s instructions.
- Pour the solution into the water reservoir.
- Run the machine through a cleaning cycle.
- Rinse the machine thoroughly with clean water.
- Reconnect the power and resume normal operation.
Cleaning The Condenser
The condenser helps to cool the refrigerant in the ice machine. Dust and debris can reduce its efficiency.
- Turn off the ice machine and disconnect the power supply.
- Locate the condenser coils, usually at the back or bottom of the machine.
- Use a soft brush or vacuum to remove dust and debris.
- If the coils are very dirty, use a coil cleaner spray.
- Ensure the coils are dry before reconnecting the power.
- Turn the machine back on and check for proper operation.
Regular cleaning of the condenser helps maintain efficient cooling and ice production.
Component Inspection
Proper component inspection is vital for diagnosing issues with an Ice O Matic ice machine. Knowing how to check each component can save time and ensure your machine runs smoothly. Let’s dive into specific components such as the thermostat and the water pump.
Checking The Thermostat
The thermostat controls the ice machine’s temperature. A malfunctioning thermostat can result in poor ice production.
Here’s a simple way to check:
- Unplug the ice machine.
- Locate the thermostat, usually near the compressor.
- Use a multimeter to test the thermostat’s continuity. Set the multimeter to the ohm setting.
- If the multimeter reads zero or infinity, the thermostat may be faulty and needs replacement.
Inspecting The Water Pump
The water pump circulates water over the evaporator plate to form ice. Issues with the water pump can lead to low ice production or no ice at all.
Follow these steps for inspection:
- Turn off and unplug the ice machine.
- Remove the front panel to access the water pump.
- Check for any visible signs of wear or damage.
- Listen for unusual noises when the machine is running. This can indicate pump issues.
- Ensure there are no blockages in the water lines connected to the pump.
If you find any problems with the water pump, consider replacing it to restore proper functionality.
Advanced Troubleshooting
Advanced troubleshooting for your Ice O Matic ice machine can save time and money. Understanding the common issues helps keep the machine running smoothly. This section covers two primary areas: electrical issues and mechanical failures.
Electrical Issues
Electrical problems can cause the ice machine to stop working. Here are some common electrical issues and solutions:
- Power Supply: Ensure the machine is plugged in and the outlet works.
- Fuse or Circuit Breaker: Check if the fuse is blown or the circuit breaker is tripped. Replace the fuse or reset the breaker if necessary.
- Wiring: Inspect the wiring for any visible damage or loose connections. Tighten or replace any faulty wires.
- Control Board: The control board manages the machine’s functions. If it fails, the machine may not operate. A professional technician should inspect and replace it if needed.
Mechanical Failures
Mechanical failures can also disrupt ice production. Here are some common mechanical issues and their solutions:
- Water Supply: Ensure there is a consistent water supply. Check for blocked or kinked water lines.
- Ice Maker Assembly: Inspect the ice maker assembly for broken or worn parts. Replace any damaged components.
- Evaporator Plate: The evaporator plate needs to be clean. Scale buildup can hinder ice production. Clean the plate using a manufacturer-recommended cleaner.
- Compressor: The compressor is crucial for cooling. If it fails, the machine won’t produce ice. A technician should inspect and repair or replace the compressor.
Regular maintenance can prevent many of these issues. Keep your Ice O Matic ice machine in top condition by addressing problems promptly.

Credit: www.youtube.com
Error Codes
Ice O Matic ice machines are known for their reliability. Yet, they can sometimes show error codes. These codes help identify problems. Understanding these codes is crucial for troubleshooting.
Deciphering Codes
Each Ice O Matic error code points to a specific issue. Here are some common codes:
Error Code | Meaning |
---|---|
E1 | Water supply issue |
E2 | High-temperature warning |
E3 | Ice bin full |
E4 | Low refrigerant |
Resetting The Machine
Sometimes, resetting the machine can clear the error codes. Follow these steps:
- Turn off the ice machine.
- Unplug the machine from the power source.
- Wait for 5 minutes.
- Plug the machine back in.
- Turn on the machine.
If the error persists, further diagnosis may be needed. Consult the user manual or contact a technician.
Maintenance Tips
Maintaining your Ice O Matic ice machine is essential for optimal performance. Regular maintenance extends the machine’s lifespan and ensures it produces clean, high-quality ice. Follow these tips to keep your ice machine running smoothly.
Regular Cleaning
Clean your ice machine regularly to prevent buildup and ensure efficiency. Follow these steps:
- Turn off and unplug the machine.
- Remove all ice from the bin.
- Use a mixture of warm water and mild detergent.
- Clean the interior surfaces with a soft cloth.
- Rinse thoroughly to remove any soap residue.
- Wipe down the exterior with a damp cloth.
For stubborn stains, use a mixture of vinegar and water. This helps remove mineral deposits.
Scheduled Inspections
Regular inspections help identify issues early. Schedule inspections at least twice a year. Focus on these areas:
- Filters: Check and replace filters as needed. Clean filters improve water quality and ice production.
- Water Lines: Inspect for leaks or blockages. Clear any clogs to ensure proper water flow.
- Condensers: Clean condenser coils to prevent overheating. Use a soft brush or vacuum to remove dust and debris.
- Evaporator Plates: Check for scale buildup. Clean with a nickel-safe cleaner if necessary.
During inspections, also check the overall condition of the machine. Look for any signs of wear and tear.
Maintaining your Ice O Matic ice machine ensures it runs efficiently. Regular cleaning and scheduled inspections are crucial for long-term performance. Follow these tips to keep your ice machine in top condition.

Credit: kitchen.manualsonline.com
When To Call A Professional
Ice O Matic ice machines are durable and efficient. But sometimes they face issues that require expert attention. Knowing when to call a professional can save you time and money. Below are key signs and tips for choosing a repair service.
Signs Of Major Issues
Understanding the signs of major issues can prevent further damage. Keep an eye out for these symptoms:
- No Ice Production: If your machine stops making ice entirely, it’s a clear sign.
- Strange Noises: Unusual sounds can indicate mechanical problems.
- Water Leaks: Leaks can lead to bigger issues like mold or electrical faults.
- Poor Ice Quality: If ice is cloudy or tastes bad, there might be a filtration issue.
- Frequent Cycles: The machine running too often could signal a malfunction.
Choosing A Repair Service
Selecting the right repair service is crucial for a quick fix. Here are some tips:
- Check Reviews: Look for customer feedback online to gauge service quality.
- Certifications: Ensure the service is certified to handle Ice O Matic machines.
- Experience: Choose a service with extensive experience in ice machine repairs.
- Warranty: A good repair service offers warranty on parts and labor.
- Response Time: Quick response times can prevent further machine damage.
Following these guidelines can help you maintain your Ice O Matic ice machine. Trust experts when major issues arise. Your machine will be back to perfect condition in no time.
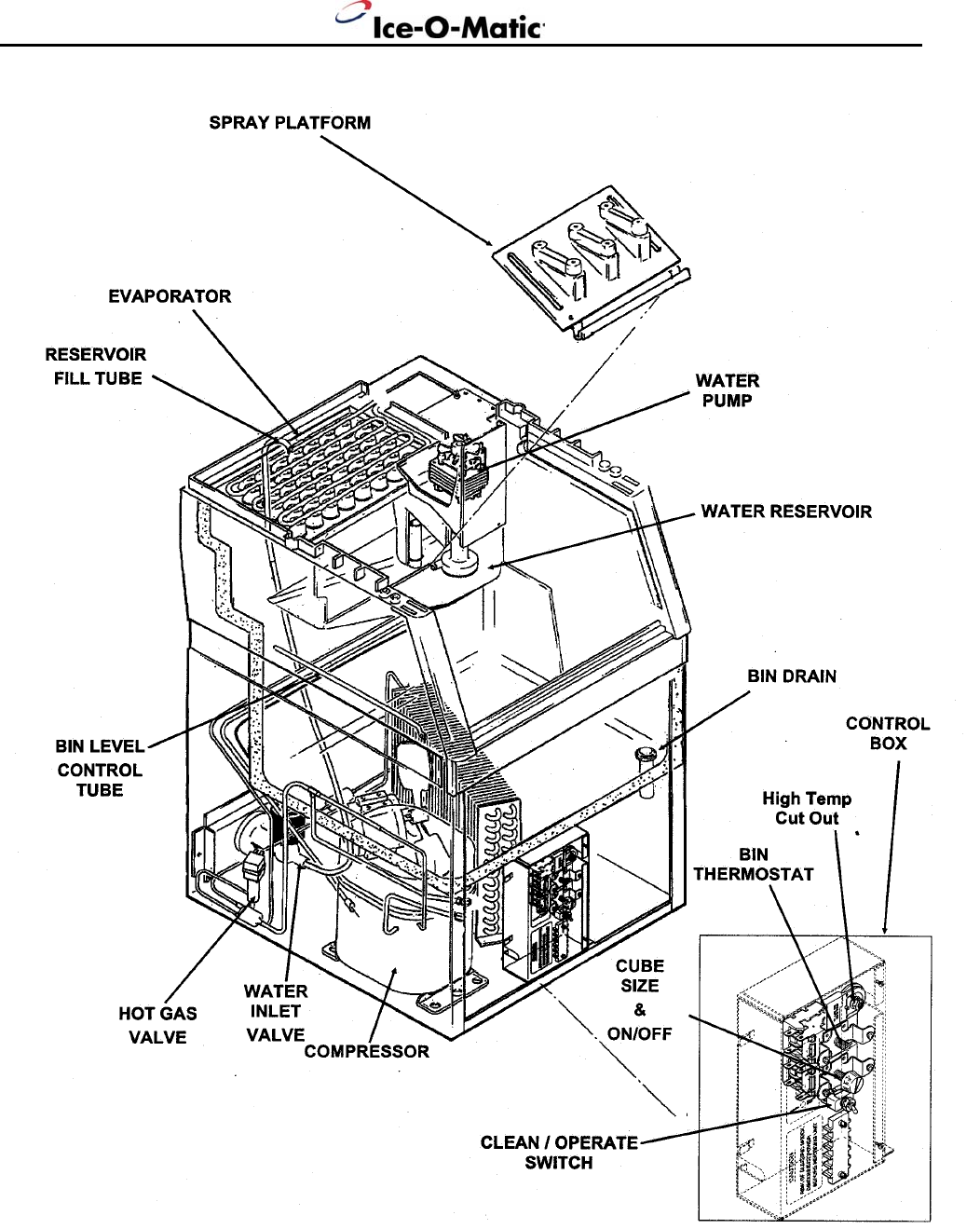
Credit: kitchen.manualsonline.com
Frequently Asked Questions
How Do I Reset My Ice O Matic Ice Machine?
To reset your Ice O Matic ice machine, turn off the power. Wait for 10 seconds. Turn it back on. This process will reset the system.
Why Is My Ice O Matic Not Making Ice?
If your Ice O Matic isn’t making ice, check for water supply issues. Ensure the machine is clean and free of obstructions. Verify power connections are secure.
How Often Should I Clean My Ice O Matic?
Clean your Ice O Matic ice machine every six months. Regular cleaning ensures efficient operation. Follow the manufacturer’s guidelines for the best results.
What Causes Ice O Matic To Leak Water?
Water leaks in Ice O Matic machines can be due to clogged filters, loose connections, or damaged hoses. Regular maintenance can help prevent leaks.
Conclusion
Troubleshooting your Ice O Matic ice machine can be simple. Follow the steps outlined for common issues. Regular maintenance helps prevent problems. Clean the machine often. Check for blockages and leaks. Ensure the water supply is steady. Always consult the user manual for guidance.
If problems persist, call a professional. Keeping your ice machine in good condition ensures a steady supply of ice.