Ice O Matic machines are essential for many businesses. But, they can face issues.
Welcome to our Ice O Matic Troubleshooting Manual. Whether you run a restaurant, cafe, or bar, a reliable ice machine is crucial. But, like any appliance, these machines can sometimes malfunction. Understanding the common problems and how to fix them can save time and money.
In this guide, we will help you identify issues and provide easy-to-follow solutions. Our aim is to keep your Ice O Matic running smoothly. Stay tuned to learn how to troubleshoot like a pro.

Credit: partsfe.com
Common Issues
Ice O Matic machines are reliable, but problems can occur. This section addresses the common issues users face. We will cover the most frequent problems and their solutions.
No Ice Production
If your Ice O Matic machine is not producing ice, check these factors:
- Power Supply: Ensure the machine is plugged in and the outlet is working.
- Water Supply: Verify the water line is connected and the valve is open.
- Filters: Clean or replace clogged filters.
- Temperature: Ensure the ambient temperature is within the recommended range.
If these steps do not resolve the issue, consult the manual for further troubleshooting.
Slow Ice Production
Slow ice production can result from various factors. Check the following:
- Water Pressure: Ensure the water pressure is adequate. Low pressure can affect ice production.
- Dirty Components: Clean the evaporator plate and other machine parts regularly.
- Ice Bin: Make sure the ice bin is not full. A full bin can halt production.
- Maintenance: Regular maintenance ensures optimal performance. Follow the maintenance schedule in the manual.
Addressing these points can significantly improve your machine’s performance.
Water Supply Problems
Ice O Matic machines rely on a consistent water supply to function correctly. Water supply issues can greatly affect the ice production process. Identifying and solving these problems is crucial for maintaining your machine’s efficiency.
Low Water Pressure
Low water pressure can cause insufficient ice production. This issue usually stems from faulty plumbing or restricted water flow.
To troubleshoot low water pressure:
- Check the incoming water line for any kinks or leaks.
- Ensure the water valve is fully open.
- Inspect the water pressure regulator. It should be set between 20-60 psi.
If these steps don’t resolve the issue, consider consulting a professional plumber.
Clogged Water Filter
A clogged water filter can hinder water flow, leading to poor ice production. Regular filter maintenance is key to avoiding this issue.
To address a clogged water filter:
- Turn off the water supply.
- Remove the water filter according to the manufacturer’s instructions.
- Inspect and clean the filter, or replace it if necessary.
- Reinstall the filter and turn the water supply back on.
Regularly replacing the water filter every six months can help prevent clogs and ensure optimal performance.
Electrical Issues
Experiencing electrical issues with your Ice O Matic machine can be frustrating. Identifying and resolving these problems quickly is essential. This guide will help you troubleshoot common electrical issues, ensuring your machine runs smoothly.
Power Supply Check
The first step is to check the power supply. Ensure the machine is plugged in securely. Verify the outlet is functioning by testing it with another device. If the outlet works, check the machine’s power cord for any visible damage or wear.
Step | Action |
---|---|
1 | Check the power cord for damage. |
2 | Ensure the machine is plugged in securely. |
3 | Test the outlet with another device. |
If the power supply is intact, the next step involves inspecting the internal components. Use a multimeter to measure the voltage. This helps determine if the power is reaching the necessary parts of the machine.
Faulty Wiring
Faulty wiring can cause many electrical issues. Start by examining the wiring within the machine. Look for loose connections, frayed wires, or any signs of burning.
- Inspect all connections thoroughly.
- Tighten any loose connections.
- Replace any damaged wires.
If you find any damaged wiring, it should be replaced immediately. This prevents further issues and ensures the safety of your machine.
In cases where the wiring seems intact, the issue might lie with the internal components. For this, consult the machine’s manual for specific troubleshooting steps. If needed, consider contacting a professional technician.
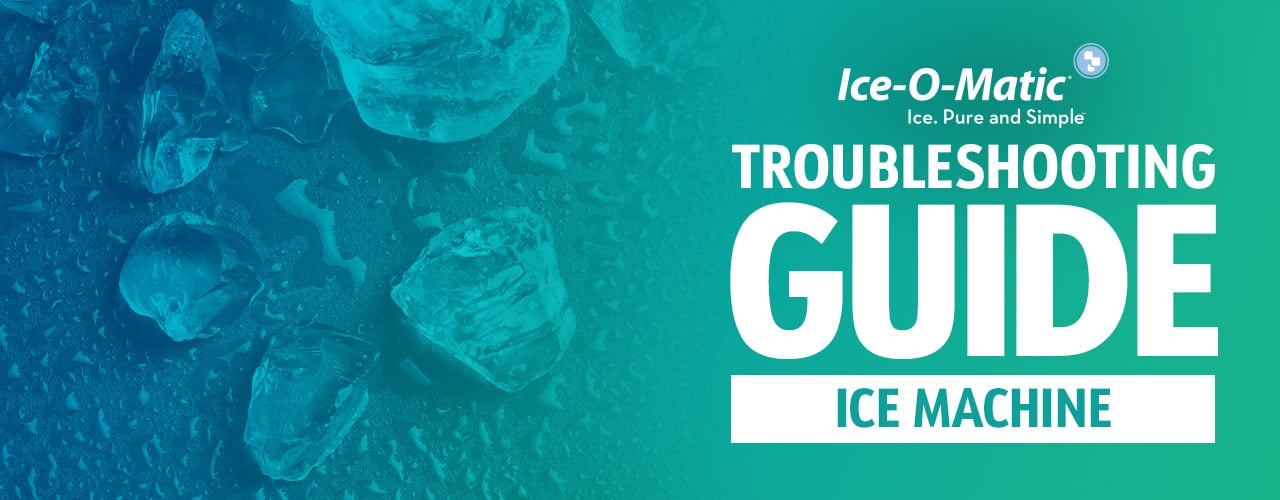
Credit: www.webstaurantstore.com
Ice Quality Concerns
Having issues with your Ice O Matic ice machine? One common problem is ice quality. This can include cloudy ice, off-tasting ice, and other concerns. This guide will help you troubleshoot and resolve these issues.
Cloudy Ice
Cloudy ice can be unappealing. It often indicates impurities in the water or air trapped inside the ice.
- Check Water Filters: Replace any old or dirty water filters. Clean water is key to clear ice.
- Inspect Water Supply: Ensure the water supply is clean and free of minerals.
- Proper Freezing Process: Make sure the freezing process is not too fast. Slow freezing helps impurities settle before freezing.
Addressing these points can often clear up the issue. If not, consider contacting a professional for further assistance.
Off-tasting Ice
Off-tasting ice can ruin beverages. It usually stems from issues with the water supply or the ice machine itself.
- Clean the Machine: Regularly clean the ice machine to prevent mold and bacteria buildup.
- Replace Water Filters: Old filters can affect the taste of the ice.
- Check Water Quality: Use filtered water to improve taste. Test the water for impurities.
Improving these factors can significantly enhance ice taste. If the problem persists, it may be time for a deeper inspection or professional help.
Maintenance Tips
Keeping your Ice O Matic machine in top condition is crucial for its longevity and efficiency. Regular maintenance ensures that your ice maker continues to produce clear and clean ice. Below, you will find essential maintenance tips that will help keep your Ice O Matic machine running smoothly.
Regular Cleaning
Regular cleaning is vital for maintaining the performance of your ice machine. Follow these steps to keep your unit clean:
- Turn off and unplug the machine before cleaning.
- Remove ice from the bin and discard it.
- Use a soft cloth and a mild detergent to clean the exterior.
- Rinse with clean water and dry with a soft towel.
- For the interior, use a mixture of water and ice machine cleaner.
- Follow the manufacturer’s instructions for the cleaning solution.
Performing these steps every few weeks helps prevent mold and scale buildup.
Descaling Procedures
Descaling your Ice O Matic machine is essential to remove mineral deposits. Follow these descaling procedures:
- Turn off and unplug the machine.
- Drain any water from the machine.
- Mix a descaling solution as per the manufacturer’s instructions.
- Pour the solution into the water reservoir.
- Run the machine for a cycle to distribute the solution.
- Turn off the machine and let it sit for 30 minutes.
- Drain the solution and rinse the machine thoroughly with clean water.
- Run a few cycles with fresh water to ensure all residues are removed.
Descaling should be done every three to six months, depending on the hardness of your water.
Regular maintenance of your Ice O Matic machine, including cleaning and descaling, ensures that it operates efficiently and produces high-quality ice. These simple steps will prolong the life of your ice maker and keep it running smoothly.
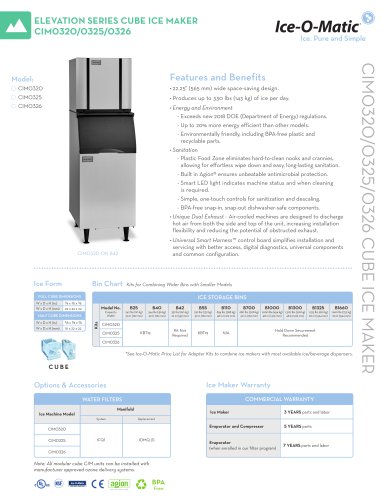
Credit: pdf.archiexpo.com
Component Checks
When troubleshooting your Ice O Matic machine, it’s crucial to perform thorough component checks. These checks help identify any underlying issues that might be affecting your ice maker’s performance. Below, we dive into the essential steps for inspecting key components such as the thermostat and compressor.
Thermostat Calibration
The thermostat is vital in regulating the temperature of your ice maker. Proper calibration ensures efficient ice production. Follow these steps to check and calibrate the thermostat:
- First, turn off the machine and unplug it.
- Locate the thermostat, usually near the control panel.
- Use a screwdriver to adjust the calibration screw.
- Turn the screw slightly clockwise to lower the temperature.
- Turn the screw counterclockwise to raise the temperature.
- Test the machine to see if the issue is resolved.
If the thermostat is still not functioning properly, it may need replacement.
Compressor Inspection
The compressor is the heart of your ice machine, responsible for cooling. Regular inspection ensures its longevity and efficiency. Here’s how to inspect the compressor:
- Unplug the ice maker before starting the inspection.
- Remove the back panel to access the compressor.
- Check for any visible signs of wear or damage.
- Ensure all connections are tight and secure.
- Listen for unusual noises which could indicate a problem.
If you find any issues with the compressor, consult a professional for repairs.
Regular component checks can significantly extend the life of your Ice O Matic machine. These inspections are simple yet effective in maintaining optimal performance.
Error Codes
Encountering error codes on your Ice O Matic machine can be frustrating. These codes help identify specific problems within the system. Understanding and resolving these errors ensures your ice maker runs smoothly.
Understanding Error Codes
Error codes display on the machine’s screen. Each code represents a different issue. Refer to the manual to decode each error. Here’s a list of common error codes and their meanings:
Error Code | Meaning |
---|---|
E1 | Water supply error |
E2 | Ice full sensor error |
E3 | Ice making error |
E4 | High-temperature error |
Identifying these codes helps in quick troubleshooting. Always consult the manual for detailed information.
Resetting The System
Sometimes, a simple reset can resolve many issues. Follow these steps to reset your Ice O Matic machine:
- Turn off the machine and unplug it.
- Wait for five minutes.
- Plug the machine back in and turn it on.
If the error persists, further troubleshooting might be needed. Keep the manual handy for specific reset instructions.
Regular maintenance reduces the chances of encountering error codes. Clean the machine and check for any visible issues regularly.
When To Call A Professional
Understanding when to call a professional for your Ice O Matic machine is crucial. This can save you time, money, and ensure your machine operates efficiently. Below, we discuss key indicators and steps to take.
Identifying Major Issues
Sometimes, your Ice O Matic machine may show signs of serious problems. These issues often require professional intervention. Here are some major issues to look out for:
- No ice production despite the machine running.
- Unusual noises coming from the machine.
- Water leakage around the machine.
- Electrical issues like tripping circuit breakers.
These problems often indicate deeper mechanical or electrical faults. Attempting to fix these without proper knowledge can be risky.
Finding A Qualified Technician
Once you identify major issues, the next step is finding a qualified technician. Here are some tips to help you find the right professional:
- Search for certified technicians who specialize in Ice O Matic machines.
- Check online reviews and customer feedback for credibility.
- Ask for references from friends or colleagues.
- Ensure they offer a warranty on their repairs.
Hiring a skilled technician ensures your Ice O Matic machine gets the right care. This can extend the lifespan of your machine and ensure it runs smoothly.
Remember, timely professional help can prevent minor issues from becoming major problems.
Frequently Asked Questions
How To Reset Ice O Matic Machine?
To reset your Ice O Matic machine, turn it off and unplug it. Wait for 5 minutes, then plug it back in and turn it on.
Why Is My Ice O Matic Not Making Ice?
Your Ice O Matic may not be making ice due to water supply issues, a clogged filter, or a malfunctioning component. Check these areas first.
How To Clean Ice O Matic Ice Maker?
To clean your Ice O Matic ice maker, use a mixture of water and ice machine cleaner. Follow the manufacturer’s instructions for best results.
What Causes Ice O Matic To Leak?
Ice O Matic machines can leak due to a faulty water line, a clogged drain, or a damaged component. Inspect these areas for issues.
Conclusion
Maintaining your Ice O Matic machine is crucial. Regular checks prevent major issues. This guide helps you troubleshoot common problems easily. Follow the steps, keep your machine clean, and ensure proper function. A well-maintained machine ensures ice availability. Stay proactive with maintenance.
Troubleshooting doesn’t have to be difficult. With this guide, you’ll handle minor issues confidently. Keep your Ice O Matic in top shape. Enjoy hassle-free operation and reliable ice production.