Magnum inverters are essential for reliable power supply. They convert DC to AC power efficiently.
Experiencing issues with your Magnum inverter can be frustrating. Whether it’s a power failure or an error code, troubleshooting is key. Understanding common problems and solutions can save time and stress. This guide will help you identify and resolve issues with your Magnum inverter.
We will explore typical problems, offer practical tips, and provide easy-to-follow solutions. By the end, you will be better equipped to handle any inverter challenges. Let’s dive into the world of Magnum inverter troubleshooting together.
Introduction To Magnum Inverters
Magnum Inverters are crucial devices in many power systems. They convert direct current (DC) to alternating current (AC). This ensures the smooth running of various electrical appliances. Understanding these devices can help in maintaining their efficiency. It also aids in troubleshooting issues when they arise.
What Are Magnum Inverters?
Magnum Inverters are power conversion devices. They are used in off-grid and mobile applications. These inverters change DC from batteries into usable AC power. This allows the operation of standard electrical devices. They are widely used in RVs, boats, and remote locations.
Importance Of Proper Functioning
Proper functioning of Magnum Inverters ensures a steady power supply. This is vital for the operation of electrical appliances. Efficient inverters prevent power interruptions. They also protect appliances from damage. Regular checks and maintenance are important. This helps in identifying potential issues early. It ensures the longevity of the inverter and connected devices.

Credit: rvcastaways.com
Common Issues With Magnum Inverters
Magnum inverters are reliable power sources for many households and businesses. Yet, like any device, they can face issues. This section will cover common problems and their solutions.
Power Output Problems
Power output problems are frequent with Magnum inverters. These issues can stem from various sources. The inverter might not produce the expected voltage. This could be due to a loose connection. Check all cables and connections first. Sometimes, the problem lies with the battery. Ensure the battery is fully charged and in good condition. If the battery is old, consider replacing it. Another common issue is an overloaded inverter. Make sure the connected devices do not exceed the inverter’s capacity. Overloading can cause the inverter to shut down or reduce output.
Inverter Not Turning On
An inverter not turning on can be frustrating. First, check the power source. Ensure the inverter is plugged in properly. If the power source is fine, inspect the fuse. A blown fuse can prevent the inverter from turning on. Replace the fuse if needed. Another possibility is a drained battery. Charge the battery fully and try again. Lastly, the issue might be internal. If none of the above steps work, consult a professional technician. They can diagnose and fix internal problems.
Diagnosing Power Output Problems
Diagnosing power output problems with Magnum inverters involves checking connections and ensuring proper settings. Regular maintenance helps identify issues early. Troubleshooting steps include examining error codes and verifying battery status.
Diagnosing power output problems in your Magnum Inverter can be a challenging task, but it’s essential for maintaining a reliable power supply. Understanding the root cause of these issues is the first step towards resolution. This section will guide you through the process of checking voltage levels and inspecting battery connections, ensuring your inverter functions optimally.Checking Voltage Levels
The first step in diagnosing power output problems is to check the voltage levels. Use a multimeter to measure the voltage at the inverter’s input and output terminals. The input voltage should match the voltage rating of your battery bank. If the input voltage is too low, it might indicate an issue with the battery or the connection. Conversely, if the output voltage is lower than expected, the inverter might be malfunctioning. Compare the readings with the specifications in the user manual. Accurate voltage levels ensure your inverter is working efficiently.Inspecting Battery Connections
Inspecting the battery connections is crucial to resolving power output problems. Start by turning off the inverter to avoid any electrical hazards. Check the battery terminals for any signs of corrosion or loose connections. Corroded terminals can impede the flow of electricity, causing power issues. Ensure all connections are tight and clean. Use a wire brush to remove any corrosion and apply a protective spray to prevent future build-up. Are your battery cables in good condition? Frayed or damaged cables can disrupt the power supply, leading to inconsistent inverter performance. Replace any damaged cables immediately. By regularly inspecting and maintaining your battery connections, you can prevent many common power output problems. What steps do you take to maintain your inverter? Share your experiences and tips in the comments below.Solutions For Inverter Not Turning On
If your Magnum inverter isn’t turning on, it can be a frustrating experience. But don’t worry, there are straightforward solutions you can try. Here, we’ll go through some effective troubleshooting steps to get your inverter back up and running.
Resetting The Inverter
One of the simplest yet most effective solutions is resetting the inverter. It’s like rebooting your computer when it’s acting up. To reset:
- Turn off the inverter by pressing the power button.
- Disconnect it from all power sources, including the battery and any solar panels.
- Wait for about 5 minutes. This gives the internal systems enough time to fully power down.
- Reconnect the power sources and turn the inverter back on.
This reset process often clears minor glitches that might be preventing your inverter from turning on. If it works, great! If not, there are other solutions to try.
Ensuring Proper Wiring
Proper wiring is crucial for the inverter to function correctly. Loose or improper connections can prevent it from turning on. Here’s what you can do:
- Inspect all wiring connections to ensure they are secure. Look for any signs of wear or damage.
- Check the battery connections. Ensure the positive and negative terminals are connected to the appropriate ports on the inverter.
- Verify that the fuse is intact. A blown fuse can disrupt the power supply.
Once you’ve checked the wiring, attempt to turn on the inverter again. Proper connections can often resolve the issue. Have you ever noticed how just a small detail like this can make a big difference?
If these solutions don’t work, it might be time to consult the user manual or seek professional help. What other troubleshooting tips have you found helpful for your Magnum inverter? Share your experiences in the comments below!
Handling Overload Conditions
Handling overload conditions with a Magnum inverter involves checking the load capacity and ensuring it matches the inverter’s specifications. Reduce the load or redistribute it to prevent frequent shutdowns. Always monitor the system for any signs of strain or overheating.
Handling overload conditions with your Magnum inverter can be a daunting task, especially when you’re unsure of what to look for. However, by understanding the signs of an overload and learning how to reduce the load on your inverter, you can prevent potential damage and ensure smooth operation. Let’s dive into the practical steps you can take to manage these situations effectively.Identifying Overload Signs
The first step to handling overload conditions is recognizing the signs. Your Magnum inverter will likely give you some clear indicators. Look out for warning lights or error codes on the display. These are often your first alert that something is amiss. Another common sign is an unexpected shutdown. If your inverter suddenly turns off, it could be due to an overload. You might also hear unusual noises. A high-pitched hum or buzzing sound can signal that the inverter is under too much stress.Reducing Load On Inverter
Once you’ve identified an overload, it’s time to take action. Reducing the load on your inverter can prevent further issues. Start by unplugging unnecessary devices. This simple step can quickly lighten the load. Consider staggering the use of heavy-duty appliances. Instead of running the washing machine and dryer simultaneously, use them one after the other. You can also invest in energy-efficient devices. These typically consume less power, making it easier for your inverter to handle the load. Handling overload conditions doesn’t have to be overwhelming. By staying vigilant and taking proactive steps, you can keep your Magnum inverter running smoothly and efficiently. What steps have you taken to manage overload conditions with your inverter? Share your tips and experiences in the comments!
Credit: rvcastaways.com
Fixing Temperature-related Issues
One of the most common issues with Magnum inverters is temperature-related problems. These issues can affect the performance and lifespan of your inverter. Understanding how to troubleshoot these problems can save you time, money, and frustration. Let’s dive into fixing temperature-related issues.
Ensuring Adequate Ventilation
Proper ventilation is crucial for maintaining the optimal temperature of your Magnum inverter. Is your inverter placed in a cramped space? Poor ventilation can lead to overheating.
Ensure that the area around the inverter is free from obstructions. Aim for at least a few inches of clearance on all sides.
Consider using a fan or air conditioning if the room tends to get hot. A well-ventilated space can significantly reduce the risk of overheating.
Checking For Overheating
Overheating can cause your inverter to shut down or perform poorly. Check if the unit feels unusually hot to the touch.
Inspect the inverter’s temperature sensors and cooling fans. Are they working correctly? A faulty fan can lead to overheating.
Look at the inverter’s display panel for any error codes related to temperature. These codes can give you a clue about what’s wrong.
Have you experienced temperature-related issues with your Magnum inverter? What steps did you take to resolve them? Share your experiences and tips in the comments below!
Addressing Error Codes
Addressing error codes on your Magnum inverter can seem challenging. Error codes indicate potential issues that need attention. Addressing these codes promptly ensures your system runs smoothly and efficiently. This guide will help you understand common error codes and provide steps to resolve them.
Understanding Common Error Codes
Magnum inverters use specific codes to signify different problems. Here are some of the most frequent error codes:
- E01: Low battery voltage. Indicates that the battery needs charging.
- E02: High battery voltage. Suggests an overcharging issue.
- E03: Overload. The system is drawing more power than it can handle.
- E04: Over-temperature. The inverter is too hot and needs to cool down.
Steps To Resolve Errors
Resolving error codes involves a few straightforward steps. Here’s how to address the most common issues:
- For E01: Check the battery connections and charge the battery. Ensure the charger is working correctly.
- For E02: Inspect the charging system. Reduce the input voltage if necessary.
- For E03: Lower the load on the inverter. Disconnect non-essential devices.
- For E04: Improve ventilation around the inverter. Allow it to cool before restarting.
Preventive Maintenance Tips
Keeping your Magnum inverter in top-notch condition can save you from unexpected power failures and costly repairs. Preventive maintenance is key to ensuring your inverter performs optimally. Here are some practical tips to help you maintain your Magnum inverter effectively.
Regular Inspection Routine
Establishing a regular inspection routine can help you catch potential problems before they become serious. Start by scheduling monthly checks on your inverter.
During these inspections, look for any signs of wear and tear or damage to the wires and connections. Ensure that all cables are securely connected and there are no loose parts.
Check the indicators and lights on your inverter to ensure they are functioning correctly. If you notice any irregularities, address them promptly to prevent further issues.
Keeping Inverter Clean
Dust and debris can affect the performance of your Magnum inverter. Regular cleaning is essential to keep it running smoothly.
Use a soft, dry cloth to wipe the surface of the inverter. Avoid using any liquid cleaners as they can damage the internal components.
Ensure the area around the inverter is clean and free from dust. This will improve airflow and prevent overheating, which can lead to equipment failure.
Have you ever experienced a sudden inverter shutdown during a critical moment? It’s frustrating, right? Regular maintenance can help you avoid such situations. By taking a few simple steps, you can ensure your Magnum inverter serves you efficiently for years.
When To Seek Professional Help
Experiencing repeated errors or malfunctions with your Magnum inverter? It’s time to seek professional help. An expert can quickly diagnose and fix the issue.
When it comes to troubleshooting your Magnum inverter, there are times when you simply can’t fix the issue by yourself. You need to know when it’s time to call in the professionals. This can save you time, money, and a lot of frustration.Identifying Complex Issues
Sometimes, the problem with your inverter is more than just a tripped breaker or a loose wire. If you’ve tried basic troubleshooting steps and the inverter still isn’t working, you might be dealing with a complex issue. For instance, if your inverter is overheating, shutting down unexpectedly, or showing error codes you can’t decipher, these are signs you need expert help. Complex issues often require specialized tools and knowledge. Attempting to fix them yourself could lead to further damage or even void your warranty.Finding Certified Technicians
Once you’ve identified that you need professional help, the next step is finding a certified technician. Not all repair services are created equal, and you want someone who understands Magnum inverters. Look for technicians who are certified by Magnum Energy. This ensures they have the training and experience necessary to accurately diagnose and repair your inverter. You can usually find certified technicians through Magnum Energy’s website or by asking for recommendations from friends or online forums. Don’t hesitate to ask the technician about their experience and qualifications. A good technician will be happy to share their credentials and provide references if needed. By seeking professional help at the right time, you can keep your Magnum inverter running smoothly and efficiently. Have you ever faced a situation where professional help saved your day? Share your stories and insights in the comments!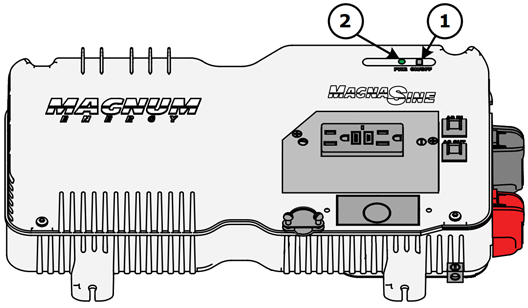
Credit: www.magnum-dimensions.com
Frequently Asked Questions
How Do I Reset A Magnum Inverter?
To reset a Magnum inverter, press and hold the “Power” button for 15 seconds until the display turns off. Release the button, wait 10 seconds, then press “Power” again to restart the inverter. Ensure all connected devices are powered off before resetting.
What Are The Common Faults Of An Inverter?
Common inverter faults include battery issues, overheating, faulty connections, and software errors. Regular maintenance can prevent these problems.
Where Is The Reset Button On An Inverter?
The reset button on an inverter is usually located near the power switch or on the front panel. Check the user manual for exact location.
Why Is My Magnum Inverter Not Turning On?
Your Magnum inverter may not turn on due to a tripped breaker, loose connections, or a faulty battery. Check and reset the breaker, tighten connections, and ensure the battery is charged and functional.
How Do I Reset My Magnum Inverter?
To reset your Magnum inverter, hold the “ON/OFF” button for 5 seconds.
Conclusion
Troubleshooting your Magnum inverter doesn’t have to be overwhelming. Follow these steps carefully. Check connections and settings. Inspect battery health. Understand error codes. Seek professional help if needed. Regular maintenance keeps your inverter in top shape. Ensuring your system runs smoothly saves time and money.
Remember, a well-maintained inverter is reliable. Happy troubleshooting!