Laser shaft alignment is crucial for machine efficiency. When issues arise, troubleshooting becomes essential.
Understanding the common problems in laser shaft alignment can save time and money. Misalignment can lead to equipment failure, costly repairs, and downtime. This blog will guide you through the troubleshooting steps, ensuring your machinery runs smoothly. By addressing these issues early, you can avoid bigger problems and maintain optimal performance.
Let’s dive into the basics of laser shaft alignment troubleshooting, helping you identify and solve potential alignment issues quickly and effectively.
Common Misalignment Issues
Laser shaft alignment is a crucial process in ensuring machinery runs smoothly. Misalignment can lead to severe damage and costly repairs. Understanding common misalignment issues helps in preventing machinery downtime.
Parallel Misalignment
Parallel misalignment occurs when the shafts are not aligned properly side-by-side. This results in the shafts being out of line horizontally or vertically.
Here are some key indicators of parallel misalignment:
- Increased vibration
- Excessive wear on bearings
- Higher operating temperatures
Parallel misalignment can be detected using laser alignment tools. These tools provide accurate measurements, ensuring precise corrections.
Angular Misalignment
Angular misalignment happens when the shafts are at an angle to each other. This leads to uneven load distribution and potential damage.
Common signs of angular misalignment include:
- Uneven coupling wear
- Irregular noise levels
- Shortened equipment lifespan
To correct angular misalignment, use laser alignment tools. They help in adjusting the angle accurately, reducing the risk of equipment failure.
Both parallel and angular misalignment can be detrimental. Regular maintenance and precise alignment are key to prolonging machinery life. Always use reliable tools and methods for alignment checks.
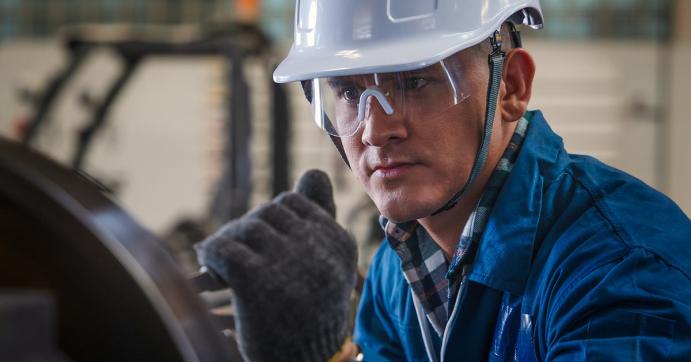
Credit: easylaser.com
Symptoms Of Misalignment
Laser shaft alignment is crucial for machine health. Misalignment can cause significant issues and lead to costly repairs. Recognizing the symptoms of misalignment early can save time and money. Below are some common symptoms of misalignment.
Vibration Issues
One of the first signs of misalignment is vibration. If machines vibrate more than usual, it can indicate an alignment problem. Vibration can harm machine components and reduce efficiency. Monitoring vibration levels helps in early detection. It is important to address this issue promptly.
Excessive Wear
Misalignment also leads to excessive wear on machine parts. Bearings, seals, and couplings wear out faster. This results in frequent replacements and higher maintenance costs. Regular inspection of these parts helps identify wear. Early intervention can prevent further damage.
Symptom | Cause | Solution |
---|---|---|
Vibration | Misaligned shafts | Realign shafts |
Excessive Wear | Improper alignment | Correct alignment |
By understanding these symptoms, you can take corrective actions. This ensures machines run smoothly and efficiently.
Tools And Equipment
Laser shaft alignment troubleshooting requires the right tools and equipment. These tools ensure precision and efficiency in aligning shafts. Without the correct equipment, you may face misalignment issues. This can lead to equipment failure and costly repairs. Let’s explore some essential tools used in laser shaft alignment.
Laser Alignment Tools
Laser alignment tools provide accurate readings. They use laser beams to measure the position of shafts. This method is faster and more precise than traditional methods. These tools come with sensors and display units. The sensors measure the alignment, and the display shows the results. Using these tools reduces human error. It also ensures better alignment results.
Dial Indicators
Dial indicators are another essential tool. They measure the displacement of shafts. These indicators have a needle that moves with the shaft. The needle shows the amount of misalignment. This helps in making precise adjustments. Dial indicators are simple yet effective. They are often used in mechanical alignment tasks. Despite being manual, they offer high accuracy.

Credit: easylaser.com
Step-by-step Alignment Process
Laser shaft alignment troubleshooting can seem complex. Following a step-by-step alignment process helps simplify it. This process ensures accurate results and reduces machine downtime. Let’s explore the key steps involved.
Preparation
Before starting, gather all necessary tools. Ensure the laser alignment system is working correctly. Clean the machine shafts to remove dirt and debris. Check for any visible damage on the shafts. This step is crucial to avoid errors during measurement.
Measurement
Attach the laser alignment tool to both shafts. Make sure the tool is secure. Turn on the laser and ensure it’s properly aligned. Record the initial readings. Rotate the shafts to different positions and take multiple measurements. This helps in identifying any misalignment accurately.
Analyze the data collected. Compare the readings with the manufacturer’s alignment specifications. Identify the type and degree of misalignment. Use this information to make the necessary adjustments. Repeat the measurement process to confirm the alignment correction.
Tips For Accurate Alignment
Achieving accurate laser shaft alignment is vital for equipment performance. Proper alignment reduces wear, vibrations, and energy consumption. Follow these tips for the best results.
Environmental Factors
Environmental conditions can affect laser shaft alignment. Temperature changes can cause metal parts to expand or contract. Perform alignment in stable temperatures to ensure accuracy.
Vibrations from nearby machines can also disrupt alignment. Turn off nearby machinery to avoid interference. Keep the work area clean and free of dust. Dust can block the laser beam and affect readings.
Environmental Factor | Impact on Alignment | Solution |
---|---|---|
Temperature | Metal expansion/contraction | Align in stable temperatures |
Vibrations | Disrupts readings | Turn off nearby machines |
Dust | Blocks laser beam | Keep area clean |
Regular Maintenance
Regular maintenance is key for accurate alignment. Check alignment tools before use. Ensure they are calibrated and functioning well. Replace damaged or worn-out tools.
Lubrication of machine parts is necessary. Lubricated parts move smoothly, helping with alignment. Inspect machines regularly for wear and tear. Address issues promptly to avoid alignment problems.
- Check and calibrate alignment tools
- Replace damaged tools
- Lubricate machine parts
- Inspect machines regularly
- Address issues promptly

Credit: ludeca.com
Frequently Asked Questions
What Is Laser Shaft Alignment?
Laser shaft alignment is a precision method for aligning shafts. It uses laser beams to ensure accurate alignment. This prevents machinery misalignment and reduces wear.
Why Is Laser Shaft Alignment Important?
Proper alignment reduces wear and tear on machinery. It increases efficiency and extends equipment lifespan. Misalignment can lead to costly repairs.
How Does Laser Shaft Alignment Work?
Laser shaft alignment uses laser beams and detectors. It measures misalignment between two shafts. The system provides real-time adjustments and accurate measurements.
What Are The Common Issues In Laser Shaft Alignment?
Common issues include incorrect setup, environmental factors, and equipment vibration. Misalignment can also occur from thermal expansion or wear.
Conclusion
Effective laser shaft alignment troubleshooting ensures smooth machinery operation. It reduces downtime and saves costs. Always follow the manufacturer’s guidelines for best results. Regular maintenance checks prevent future alignment issues. Stay proactive with alignment tools and techniques. Your machinery will thank you.
Remember, precision matters in alignment tasks. Keep learning and improving your skills. Proper alignment boosts efficiency and productivity. Happy aligning!