Dealing with the Easy-Laser XT660 alignment tool can sometimes present challenges. Understanding how to troubleshoot common issues can save you time and frustration.
The Easy-Laser XT660 is a reliable tool for shaft alignment. Yet, even the best tools can experience occasional problems. If you find yourself stuck with alignment issues, this guide is here to help. We will walk you through the common problems and their solutions.
Troubleshooting doesn’t have to be complex. With a bit of knowledge, you can resolve most issues quickly. Let’s dive into the troubleshooting steps to keep your Easy-Laser XT660 running smoothly.
Common Issues
The Easy-Laser XT660 is a powerful tool for alignment tasks, but like any device, it can encounter issues. Understanding common problems can help you troubleshoot quickly and keep your project on track.
Device Not Turning On
If your Easy-Laser XT660 is not turning on, check the following:
- Battery: Ensure the battery is charged. Connect the device to a power source and check if the charging indicator lights up.
- Power Button: Press and hold the power button for at least 3 seconds. Sometimes a brief press does not activate the device.
- Connections: Verify all connections are secure and clean. Loose or dirty connectors can prevent the device from powering on.
Display Problems
Display issues can range from a blank screen to distorted images. Consider these steps:
- Brightness Settings: Adjust the brightness settings. A low brightness level can make the screen appear blank.
- Screen Calibration: Recalibrate the screen if the touch response is inaccurate. Follow the instructions in the user manual.
- Software Updates: Ensure the device software is up to date. Outdated software can cause display malfunctions.
Here is a quick reference table for troubleshooting display problems:
Issue | Possible Solution |
---|---|
Blank Screen | Check brightness settings, charge the battery |
Distorted Images | Update software, check connections |
Unresponsive Screen | Recalibrate, restart the device |
Calibration Errors
Calibration errors can be frustrating when working with the Easy-Laser Xt660. These issues can lead to incorrect readings and calibration failure, disrupting your tasks. Understanding these errors is essential for smooth operation. Let’s delve into some common problems and their solutions.
Incorrect Readings
Incorrect readings often arise from calibration errors. This can be due to improper sensor placement or environmental factors. Ensure sensors are securely attached. Verify that the surface is clean and free from debris. Calibration errors can also result from interference. Keep the area clear of electronic devices that may cause disruptions.
Calibration Failure
Calibration failure typically occurs when the device cannot complete its calibration process. This may be due to low battery levels. Always check the battery before starting. Another common issue is outdated software. Regularly update the Easy-Laser Xt660 software to avoid this problem. Check connections and ensure all components are properly aligned and secured.
Laser Alignment Problems
Laser alignment problems can disrupt operations and cause significant downtime. The Easy-Laser Xt660 is a reliable tool, but issues can still arise. Addressing these problems quickly ensures smooth operations and reduced downtime. This section explores common laser alignment issues and their solutions.
Misalignment Detection
Misalignment is a frequent problem in laser alignment. The Easy-Laser Xt660 helps detect misalignment with precision. Misalignment happens when the laser beams don’t align properly with the target. This can be due to several factors like equipment vibration or improper setup.
To fix this, start by checking the setup. Ensure the laser and targets are firmly mounted. Make sure there is no movement during alignment. Regularly calibrate the Easy-Laser Xt660 to maintain accuracy. This helps in detecting and correcting misalignment quickly.
Beam Intensity Issues
Beam intensity issues can affect the accuracy of laser alignment. The laser beam may become weak or unfocused. This usually happens due to dirt on the laser lens or environmental factors like dust and moisture.
Clean the laser lens regularly to maintain beam intensity. Use a soft, lint-free cloth to avoid scratches. Also, ensure the working environment is clean and dry. If the beam remains weak, check the laser power source. Replace batteries if needed.
Beam intensity can also be affected by long distances. Ensure the distance between the laser and target is within the recommended range. This ensures a strong, focused beam for accurate alignment.
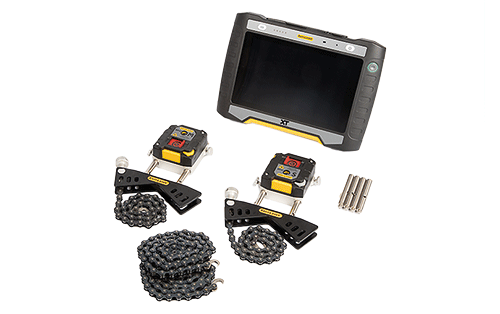
Credit: easylaser.com
Software Glitches
Experiencing software glitches with the Easy-Laser Xt660 can be frustrating. These issues can disrupt your work. This section covers common software problems and how to fix them.
App Crashes
App crashes are a common issue. They can occur for various reasons. Ensure your app is always up to date. Updates often fix bugs and improve performance.
If the app still crashes, try these steps:
- Restart your device. This can solve many temporary issues.
- Clear app cache. This can remove corrupt files causing crashes.
- Check for available storage. Low storage can lead to app crashes.
Data Syncing Issues
Data syncing issues can cause delays in your project. It’s vital to ensure all devices are correctly synced.
To address data syncing problems, follow these tips:
- Ensure all devices are connected to a stable internet connection.
- Check that the Easy-Laser Xt660 software is updated on all devices.
- Restart the app on both the sending and receiving devices.
These steps can solve most syncing problems. Always ensure your network is stable. A weak connection can disrupt data transfer.
For further assistance, consult the Easy-Laser support team. They can provide detailed solutions for complex issues.
Maintenance Tips
Keeping your Easy-Laser Xt660 in top condition ensures accurate results and extends the device’s lifespan. Here are some essential maintenance tips to help you troubleshoot effectively.
Regular Cleaning
Regular cleaning is crucial for the Easy-Laser Xt660. Dust and debris can affect its performance.
- Use a soft, lint-free cloth to wipe the device.
- Avoid using harsh chemicals or abrasives.
- Clean the laser lenses gently to maintain accuracy.
Cleaning the device regularly helps in maintaining its precision and functionality.
Battery Management
Proper battery management is vital for uninterrupted use of the Easy-Laser Xt660.
Action | Frequency |
---|---|
Charge the battery fully | After each use |
Store the battery properly | When not in use |
Check for battery wear | Monthly |
A well-maintained battery ensures the device is always ready for use.
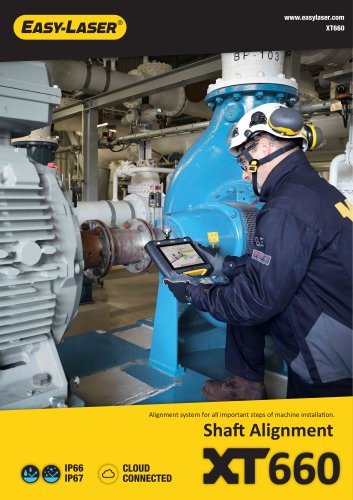
Credit: pdf.directindustry.com
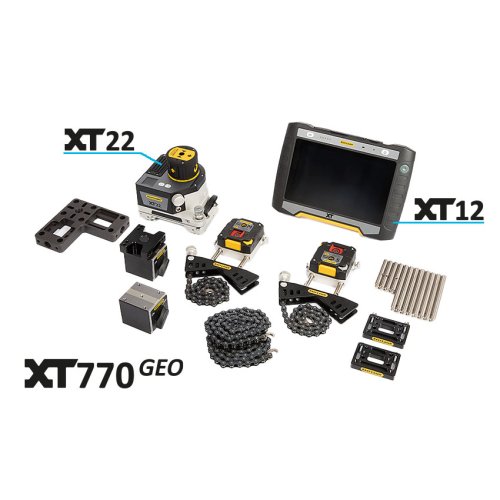
Credit: artechequipmentsupply.com
Frequently Asked Questions
How To Calibrate Easy-laser Xt660?
To calibrate the Easy-Laser Xt660, follow the steps in the user manual. Ensure the device is level and stable. Use the calibration tool provided. Make necessary adjustments until the readings are accurate.
What Does Error Code 404 Mean On Easy-laser Xt660?
Error code 404 on the Easy-Laser Xt660 indicates a connection issue. Check all cables and connections. Ensure the sensors are properly attached. Restart the device if the issue persists.
How To Update Easy-laser Xt660 Firmware?
To update the firmware of the Easy-Laser Xt660, visit the official website. Download the latest firmware version. Follow the step-by-step instructions provided. Ensure the device is fully charged before starting the update.
Why Is My Easy-laser Xt660 Not Turning On?
If your Easy-Laser Xt660 is not turning on, check the battery first. Ensure it is fully charged. Check the power button and connections. If the issue continues, contact customer support for assistance.
Conclusion
Troubleshooting the Easy-Laser Xt660 can be simple with the right steps. Follow the guide to identify and fix common issues. Regular maintenance ensures optimal performance. Always double-check connections and settings. If problems persist, consult the manual or seek expert help.
Keeping your tool in top shape saves time and effort. Stay proactive and attentive to avoid major disruptions. Happy aligning!