Facing issues with your 501K system? You’re not alone.
Many encounter challenges that need quick solutions. Understanding common problems and their fixes can save you time and stress. 501K troubleshooting can seem daunting at first. Yet, with the right guidance, it becomes manageable. This blog aims to help you navigate through these common issues.
We’ll explore practical tips and steps to resolve your 501K troubles. Whether it’s connectivity problems, data errors, or system malfunctions, we’ve got you covered. Our goal is to make troubleshooting straightforward and accessible. So, let’s dive in and tackle those 501K challenges together!
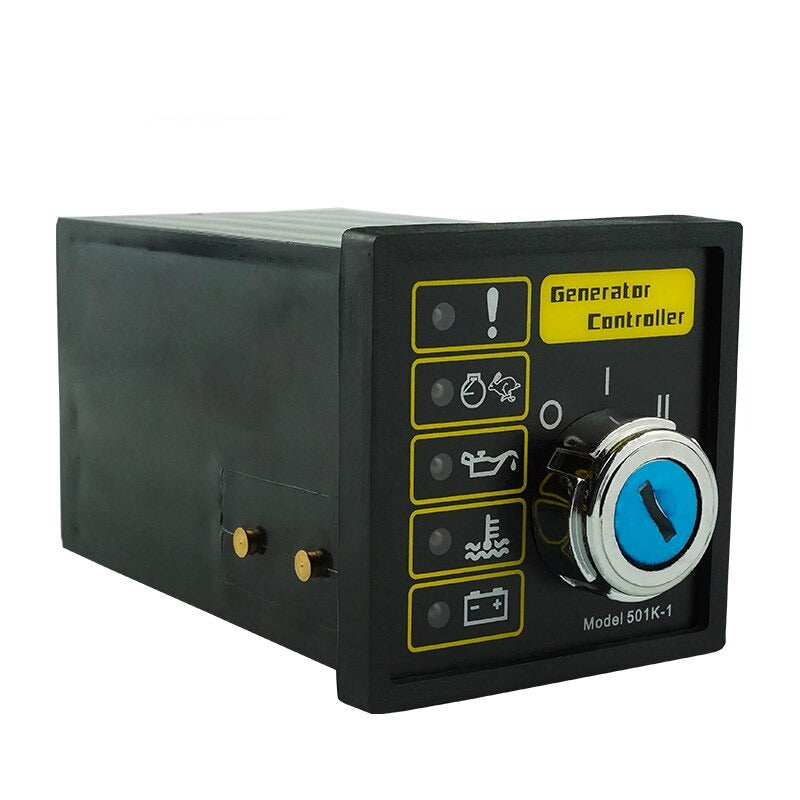
Credit: ivparts.com
Common 501k Problems
The 501K engine is a vital component in many industrial settings. Yet, it is not immune to problems. Understanding common issues can help maintain peak performance. Let’s explore the frequent problems faced by 501K engines and how to troubleshoot them.
Engine Starting Issues
Many users experience engine starting issues with their 501K engines. These issues can stem from various factors:
- Battery Problems: Weak or dead batteries can hinder engine start.
- Fuel System Issues: Clogged filters or fuel lines can block fuel flow.
- Ignition System Faults: Faulty spark plugs or ignition coils can prevent starting.
To diagnose engine starting problems, follow these steps:
- Check the battery voltage and connections.
- Inspect fuel filters and lines for blockages.
- Examine spark plugs and ignition coils for wear and tear.
Regular maintenance can prevent most starting problems. Always keep spare parts on hand for quick fixes.
Overheating
Overheating is a common issue in 501K engines. Various factors can cause the engine to overheat:
- Insufficient Coolant: Low coolant levels can lead to overheating.
- Radiator Issues: Blocked or damaged radiators can impair cooling.
- Cooling Fan Problems: Malfunctioning fans reduce cooling efficiency.
To troubleshoot overheating problems, you should:
- Check coolant levels and top up if necessary.
- Inspect the radiator for blockages or damage.
- Test the cooling fan for proper operation.
Maintaining the cooling system is crucial for preventing overheating. Regular inspections and cleaning can help.

Credit: vision-sophie.en.made-in-china.com
Diagnostic Tools
When troubleshooting 501K systems, having the right diagnostic tools is essential. These tools help identify and fix issues quickly and accurately. Two of the most important diagnostic tools are multimeters and thermal cameras. Let’s explore how each of these tools can assist in the troubleshooting process.
Multimeters
Multimeters are versatile tools used in diagnosing electrical issues. They can measure voltage, current, and resistance. This makes them valuable for checking circuit integrity and identifying faulty components. By using a multimeter, you can pinpoint where the problem lies. This saves time and effort.
To use a multimeter, first set it to the correct measurement type. For voltage, set it to volts. For current, set it to amps. For resistance, set it to ohms. Then, connect the probes to the circuit or component. Read the display to get the measurement. Compare the results with the expected values to find discrepancies.
Thermal Cameras
Thermal cameras are powerful tools for identifying temperature-related issues. They detect heat patterns and display them visually. This helps in spotting overheating components or areas with unusual heat signatures. Thermal cameras can detect problems invisible to the naked eye.
Using a thermal camera is straightforward. Turn on the camera and point it at the area to be inspected. The camera will show a thermal image on the screen. Look for hotspots or areas with different temperatures. These spots may indicate problems that need attention. Address these issues to prevent further damage or failure.
Step-by-step Troubleshooting
Troubleshooting a 501K can seem daunting. But a systematic approach makes it manageable. Follow this step-by-step guide. It breaks down the process into simple stages. This ensures you cover all bases and identify the issue efficiently.
Visual Inspection
Begin with a visual inspection. Look for obvious issues. Check for loose wires or burnt components. Examine the circuit board for discoloration. This can indicate overheating. Also, look for any signs of physical damage. Sometimes, the problem is visible. Catching it early can save time.
Component Testing
Next, test the components. Use a multimeter to check voltage and continuity. Start with the power supply. Ensure it delivers the correct voltage. Then, move to other components. Test resistors, capacitors, and transistors. Each should have specific readings. If a component fails the test, replace it. This step helps isolate the faulty part.
Preventive Maintenance
Preventive maintenance is key to keeping your 501K equipment running smoothly. This involves routine checks and scheduled upkeep. By following a preventive maintenance plan, you can avoid unexpected breakdowns and extend the lifespan of your equipment.
Regular Inspections
Regular inspections are crucial for early detection of potential issues. These inspections help you identify wear and tear before it becomes a significant problem.
During an inspection, check the following components:
- Belts and hoses
- Electrical connections
- Fluid levels
- Filters
It’s essential to log each inspection. Keeping a record helps track trends and predict future maintenance needs.
Scheduled Replacements
Scheduled replacements prevent unexpected failures. Replace parts based on the manufacturer’s recommendations. This ensures your equipment runs efficiently.
Common parts that need regular replacement include:
- Filters
- Belts
- O-rings
- Seals
Following a schedule for these replacements can save time and reduce downtime.
Here’s a sample table for tracking scheduled replacements:
Part | Replacement Interval | Last Replaced |
---|---|---|
Filters | Every 6 months | January 2023 |
Belts | Every 12 months | July 2022 |
O-rings | Every 18 months | October 2021 |
Seals | Every 24 months | January 2022 |
By following these preventive maintenance steps, you can ensure your 501K equipment stays in peak condition. Regular inspections and scheduled replacements are vital for maintaining efficiency and avoiding costly repairs.
Expert Advice
Troubleshooting 501K errors can seem daunting. Yet, with expert advice, you can resolve these issues more effectively. Here, we delve into professional insights to help you tackle these problems.
Consulting Professionals
Sometimes, the best step is to consult a professional. Experts have the experience to diagnose the issue swiftly. They can identify root causes that you might overlook. Their knowledge often leads to quicker resolutions. Consulting professionals can save you time and frustration.
Advanced Techniques
Advanced techniques can also aid in resolving 501K errors. One such technique is analyzing server logs. This helps pinpoint where the error occurs. Another useful method is testing server configurations. Correct configurations ensure smooth operation. These techniques require some technical know-how. However, they can be highly effective.

Credit: partsofgenerator.com
Frequently Asked Questions
What Is 501k Error?
A 501K error typically indicates a problem with server configuration. It prevents the server from processing the request.
How To Fix 501k Error?
To fix a 501K error, check server configuration, update software, and ensure all dependencies are correctly installed.
Why Does 501k Error Occur?
The 501K error occurs due to server misconfigurations, outdated software, or missing dependencies that disrupt server processing.
Can Outdated Software Cause 501k Error?
Yes, outdated software can lead to a 501K error by causing compatibility issues with server configurations.
Conclusion
Troubleshooting 501K issues can be straightforward with the right approach. Always start by identifying the problem. Check each component carefully. Use the solutions discussed in the blog. They are practical and easy to follow. Regular maintenance prevents most issues. Stay patient and systematic.
Fixing 501K problems ensures smooth operation. Keep this guide handy for future reference. Happy troubleshooting!