Got an Ingersoll Rand air compressor acting up? You’re not alone.
Many users face issues, but solutions are within reach. Air compressors are essential tools in many industries, from manufacturing to construction. They power various equipment and simplify tasks. But like all machines, they can encounter problems. Understanding these issues and knowing how to fix them can save time and money.
In this guide, we provide a comprehensive troubleshooting resource. This guide is designed to help you diagnose and resolve common problems. Whether it’s a pressure drop or a strange noise, our guide covers it all. Let’s dive into the solutions and get your air compressor running smoothly again.
Common Issues
Ingersoll Rand air compressors are reliable, but they can face common issues. Knowing these problems can help you troubleshoot effectively. This guide will cover two frequent issues: air leaks and overheating.
Air Leaks
Air leaks are a common problem in air compressors. They reduce efficiency and increase energy costs. Check hoses and connections for signs of wear or damage. Use soapy water to detect leaks. Apply the soapy water to suspected areas and look for bubbles. Tighten or replace any faulty components to fix the leaks.
Overheating
Overheating can damage your air compressor. It can occur due to several reasons. Check if the cooling fans are working properly. Ensure that the compressor is not placed in a confined space. Clean the air filters regularly. Dirty filters restrict airflow and cause overheating. Monitor the oil levels, as low oil can lead to increased friction and heat. Refill the oil if necessary.
Startup Problems
Startup problems with your Ingersoll Rand Air Compressor can be frustrating. These issues can delay work and reduce productivity. This guide will help you troubleshoot common startup problems. The focus will be on two main issues: the motor not starting and low voltage.
Motor Not Starting
If the motor does not start, check the power supply first. Ensure the compressor is plugged in securely. Inspect the power cord for any visible damage. A damaged cord can prevent the motor from starting.
Next, check the circuit breaker. The breaker may have tripped. Resetting it could solve the problem. Also, check the pressure switch. It might be faulty or incorrectly set. Adjust or replace it if necessary.
Another potential issue is a faulty motor capacitor. The capacitor helps start the motor. If it is defective, the motor will not start. Replace the capacitor to fix the issue.
Low Voltage
Low voltage can cause startup problems. It can prevent the motor from running. Use a multimeter to check the voltage at the power outlet. The voltage should match the compressor’s requirements.
If the voltage is too low, check the power source. Ensure there are no other heavy appliances on the same circuit. They can draw power away from the compressor. This can cause low voltage issues.
Also, inspect the extension cord if you are using one. A cord that is too long or too thin can cause voltage drops. Use a shorter or thicker cord to ensure proper voltage supply.
Pressure Problems
Pressure problems in an Ingersoll Rand air compressor can impact performance. Low or high pressure issues need quick fixes to avoid damage. Understanding these problems ensures your air compressor works efficiently.
Low Pressure
Low pressure can cause tools to work poorly. Check the air filter for clogs. Clean or replace it if dirty. Inspect the intake valve. It may be stuck or damaged. Replace faulty valves. Ensure the pressure switch is set correctly. Adjust it to the recommended level. Examine the compressor’s belts. Worn-out belts slip and reduce pressure. Replace them if needed. Leaks also cause low pressure. Listen for hissing sounds. Apply soapy water to fittings. Bubbles reveal leaks. Tighten or replace fittings to fix leaks.
High Pressure
High pressure can damage tools and the compressor. Check the pressure switch first. It might be faulty. Replace it if needed. Inspect the relief valve. It releases excess pressure. Ensure it opens at the correct pressure. Clean or replace it if it sticks. Verify the accuracy of the pressure gauge. A faulty gauge gives wrong readings. Replace it if necessary. Ensure the compressor’s cut-out pressure is set correctly. Adjust it to the manufacturer’s specifications. Examine the discharge line. It should not be blocked. Clean or replace it to ensure proper airflow.
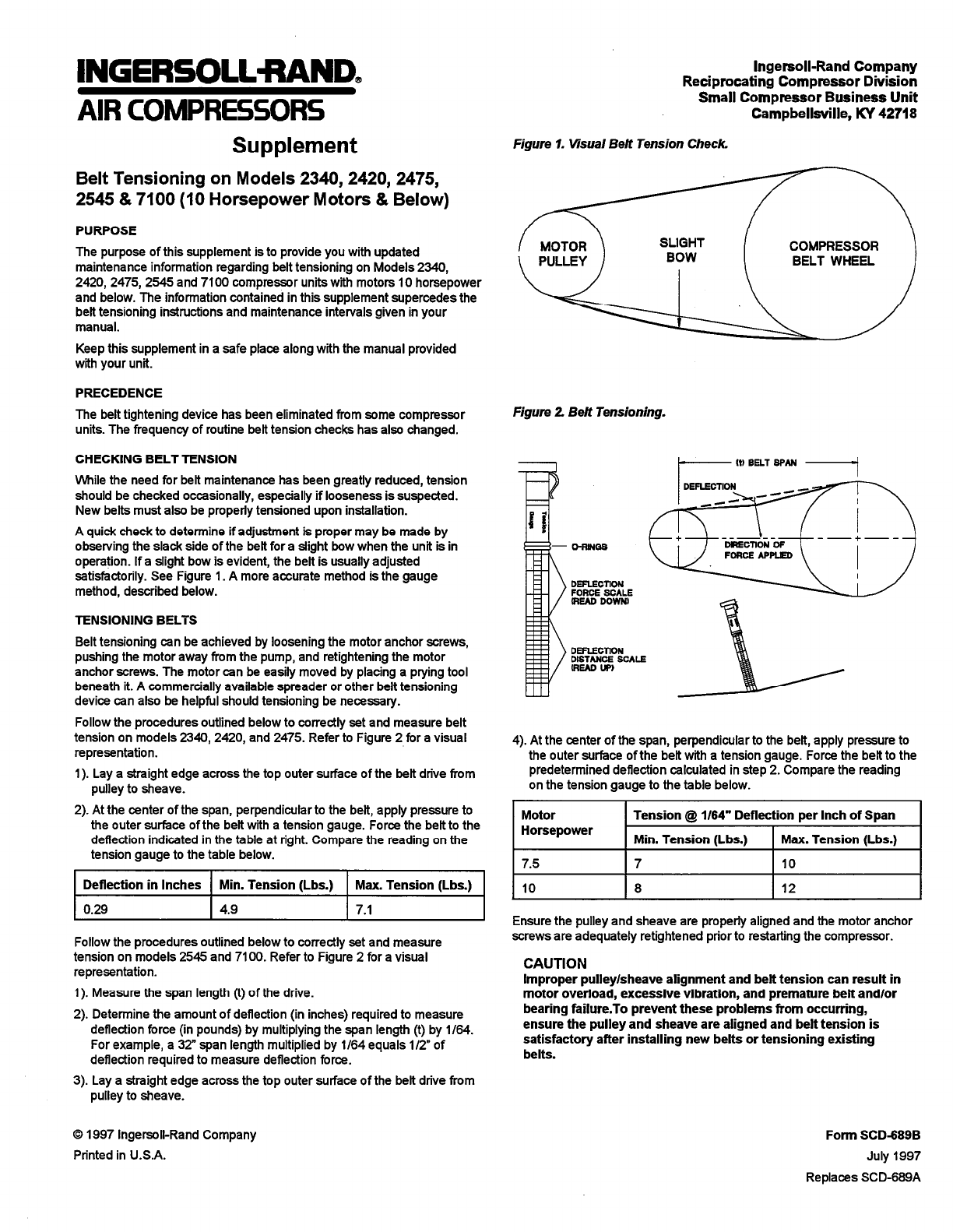
Credit: powertool.manualsonline.com
Maintenance Tips
Maintaining your Ingersoll Rand air compressor is crucial for its long life. Regular upkeep ensures efficient performance and prevents unexpected breakdowns. This section provides essential tips to keep your air compressor in top shape.
Regular Checks
Inspect your air compressor regularly. Check for unusual noises and vibrations. Look for signs of wear and tear. Ensure all nuts and bolts are tight. Examine hoses and connections for leaks. Verify the oil level and top it up if needed. Regular checks can help detect potential issues early.
Cleaning Filters
Clean the air filters frequently. Dirty filters reduce efficiency and strain the motor. Remove the filter and use compressed air to clean it. If the filter is too dirty, consider replacing it. A clean filter allows proper airflow and keeps the compressor running smoothly.
Noise Issues
Noise issues with your Ingersoll Rand Air Compressor can be frustrating. Understanding the cause can help fix it quickly. This section will guide you through identifying and resolving common noise problems.
Unusual Sounds
Unusual sounds from an air compressor can indicate various issues. Listen carefully to identify the type of noise. Different sounds can mean different problems.
- Rattling: Loose parts or fasteners. Check and tighten all bolts.
- Squealing: Worn-out belts or misalignment. Inspect and replace if needed.
- Grinding: Bearing issues. Lubricate or replace the bearings.
- Hissing: Air leaks. Check hoses and connections for leaks.
Vibration
Vibration can cause wear and tear. It is crucial to address it promptly. Here are some common causes and solutions:
Cause | Solution |
---|---|
Unbalanced Parts | Check and balance moving parts. |
Loose Mounting | Tighten mounting bolts and ensure stable placement. |
Worn Components | Inspect and replace worn-out components. |
Improper Installation | Reinstall according to the manufacturer’s guidelines. |
Regular maintenance of your air compressor can prevent noise issues. Follow the manufacturer’s maintenance schedule. Always use genuine parts for replacements.
Electrical Issues
Electrical Issues can hinder the performance of your Ingersoll Rand air compressor. Understanding these issues is crucial for proper troubleshooting. This guide will help you identify and resolve common electrical problems.
Circuit Breaker Trips
A tripping circuit breaker is a common issue with air compressors. It often indicates an overload or a short circuit. Here are some steps to diagnose this problem:
- Check if the compressor is drawing more current than the circuit can handle.
- Inspect the air compressor for any signs of short circuits.
- Ensure the breaker is the correct size for the compressor.
If the breaker trips frequently, it might be time to call a professional. Consistent tripping can damage the compressor or other electrical components.
Wiring Problems
Faulty wiring can cause various issues with your air compressor. Here’s how to check for wiring problems:
- Ensure all connections are tight and secure.
- Inspect wires for any signs of wear or damage.
- Use a multimeter to check for continuity in the wires.
Loose or damaged wires can lead to inefficient operation or complete failure. Replace any faulty wiring immediately to avoid further issues.
By following this guide, you can resolve common electrical issues and ensure your Ingersoll Rand air compressor runs smoothly.
Lubrication Problems
Dealing with lubrication problems in your Ingersoll Rand air compressor can be daunting. Proper lubrication is vital for the machine’s performance and longevity. This section addresses common lubrication issues, focusing on oil levels and the type of lubricant.
Oil Levels
Maintaining correct oil levels is essential for the smooth operation of your air compressor. Inadequate oil levels can lead to overheating and damage. Follow these steps to check the oil levels:
- Turn off the compressor and unplug it.
- Locate the oil sight glass or dipstick.
- Ensure the oil level is between the minimum and maximum marks.
If the oil level is low, top it up. Use the recommended oil type to avoid any issues.
Type Of Lubricant
The type of lubricant used in your air compressor is crucial. Using the wrong type can cause inefficiency and wear. Ingersoll Rand recommends specific oils for their compressors:
Compressor Type | Recommended Oil |
---|---|
Reciprocating | Ingersoll Rand All-Season Select |
Rotary Screw | Ingersoll Rand Ultra Coolant |
Always refer to your user manual for the correct oil. Using the specified lubricant ensures optimal performance and longevity.
Proper lubrication is key to your air compressor’s efficiency. Regular maintenance, including checking oil levels and using the right type of lubricant, can prevent many issues. Follow these guidelines to keep your Ingersoll Rand air compressor running smoothly.
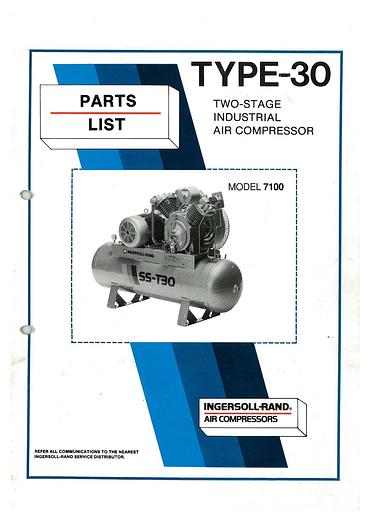
Credit: www.ngkusedmachine.com
Expert Tips
Finding an effective Ingersoll Rand Air Compressor Troubleshooting Guide Pdf can be a game-changer for maintaining your equipment. Expert tips provide valuable insights to keep your air compressor running smoothly and efficiently. Here, we delve into some practical advice under the headings of Prolonging Lifespan and Efficiency Boost.
Prolonging Lifespan
To extend the life of your Ingersoll Rand air compressor, regular maintenance is crucial. Here are some expert tips to keep your equipment in top shape:
- Check and Replace Filters: Dirty filters can strain the compressor. Change them regularly.
- Monitor Oil Levels: Check oil levels weekly. Low oil can damage the compressor.
- Inspect Belts: Worn belts reduce efficiency. Replace them if you see wear or damage.
- Clean Intake Vents: Dust and debris can block vents. Clean them to ensure proper airflow.
Efficiency Boost
Improving the efficiency of your air compressor not only saves energy but also reduces costs. Follow these expert tips to boost efficiency:
- Fix Air Leaks: Even small leaks can cause significant energy loss. Use a leak detector to find and fix them.
- Optimize Pressure Settings: Set the pressure to the lowest required level. This reduces wear and energy use.
- Regular Maintenance: Keep up with scheduled maintenance to ensure optimal performance.
- Use Proper Ventilation: Ensure the compressor room is well-ventilated. Overheating can reduce efficiency.
Adopting these tips from the Ingersoll Rand Air Compressor Troubleshooting Guide Pdf will help you maintain your air compressor effectively. Regular checks and timely maintenance keep your machine running smoothly and efficiently.
Credit: www.scribd.com
Frequently Asked Questions
How Do I Reset My Ingersoll Rand Air Compressor?
Press the reset button on the motor. Wait 30 seconds. Restart the compressor.
Why Won’t My Ingersoll Rand Air Compressor Start?
Check the power supply. Ensure the switch is on. Inspect for blown fuses or tripped breakers.
What Causes Air Compressor Overheating?
Dirty filters or lack of ventilation. Check and clean filters. Ensure proper airflow.
How Do I Fix Low Pressure In My Air Compressor?
Inspect for leaks. Tighten connections. Replace damaged hoses. Check regulator settings.
How Often Should I Service My Ingersoll Rand Air Compressor?
Every 3 months or 500 hours of use. Follow the manual’s maintenance schedule.
Conclusion
Solving issues with your Ingersoll Rand air compressor is easier now. With this guide, you can troubleshoot common problems quickly. Keep your compressor running smoothly with regular checks. Follow these steps to save time and money. Remember, a well-maintained compressor lasts longer.
Stay proactive and prevent major repairs. Use this troubleshooting guide to ensure optimal performance. Happy compressing!