Laars Mini Therm boilers are reliable and efficient. But like any equipment, they can face issues.
Troubleshooting a Laars Mini Therm boiler might seem daunting. With the right guidance, you can solve many common problems yourself. Boilers are crucial for home comfort, especially during cold months. Understanding how to fix minor issues can save time and money.
This guide will help you identify and address typical boiler issues. From strange noises to heating problems, we will cover it all. Knowing these tips can keep your boiler running smoothly. Stay warm and comfortable with a well-maintained Laars Mini Therm boiler. Let’s dive into troubleshooting steps that are simple to follow.
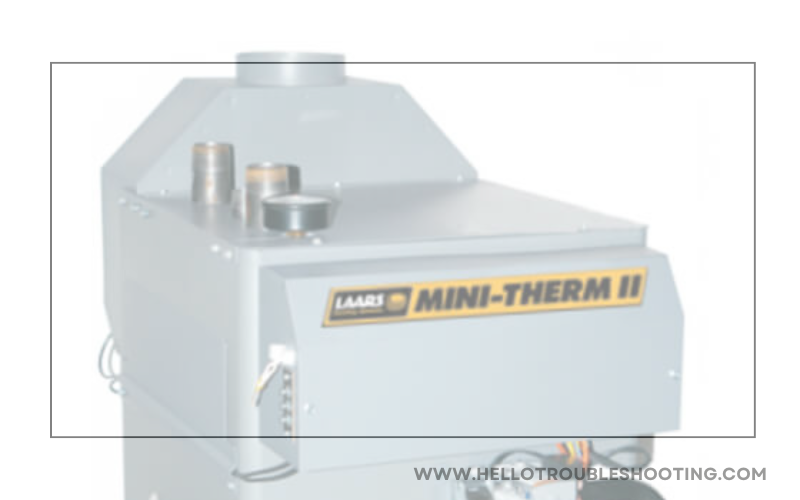
Common Boiler Issues
The Laars Mini Therm Boiler is reliable. But like all boilers, it can face some issues. Knowing the common problems can help you troubleshoot quickly. Here are some frequent issues you may encounter.
No Heat
If your Laars Mini Therm Boiler is not producing heat, it can be frustrating. Several factors could cause this issue. First, check the thermostat settings. Ensure it is set to the desired temperature. Also, confirm that the thermostat is working properly.
Next, inspect the boiler’s power supply. Verify that the boiler is plugged in and the circuit breaker is not tripped. If the boiler has power but still no heat, the pilot light might be out. Relight the pilot light according to the manufacturer’s instructions.
If these steps do not resolve the issue, there might be a problem with the burner or gas supply. This might need a professional’s help. Regular maintenance can prevent many of these problems.
Low Water Pressure
Low water pressure is another common issue with boilers. Your Laars Mini Therm Boiler might show an error code if the pressure is too low. You can check the pressure gauge on the boiler. It should read between 1 and 2 bars. If the pressure is below this range, you need to add water to the system.
Follow these steps to increase the water pressure:
- Turn off the boiler and allow it to cool.
- Locate the filling loop; this is usually a flexible hose.
- Open the valves on the filling loop to let water into the system.
- Monitor the pressure gauge and stop when it reaches the correct level.
- Close the valves and remove the filling loop.
If the pressure drops frequently, there might be a leak in the system. Inspect the pipes and connections for any signs of water. If you find a leak, it’s best to call a professional to fix it.
Maintaining the correct water pressure ensures your boiler works efficiently. Regular checks can help you avoid sudden pressure drops.
Error Codes And What They Mean
Understanding the error codes of your Laars Mini Therm Boiler is essential. They help you identify and fix problems quickly. This section explains the most common error codes and what they mean.
Understanding Error Codes
Error codes are a way for your boiler to communicate issues. Each code points to a specific problem. Knowing these codes can save you time and money. You can avoid unnecessary service calls.
Common Error Codes
Error Code | Meaning | Solution |
---|---|---|
E01 | Ignition Failure | Check gas supply. Restart boiler. |
E02 | Flame Failure | Inspect flame sensor. Clean if dirty. |
E03 | High Limit Exceeded | Check thermostat settings. Allow cooling. |
E04 | Low Water Pressure | Refill system. Check for leaks. |
E05 | Sensor Error | Inspect and replace sensors if needed. |
E01 – Ignition Failure
This code means the boiler failed to ignite. It could be due to a lack of gas supply. Check the gas valve. Make sure it is open. Restart the boiler. If the problem persists, consult a technician.
E02 – Flame Failure
The flame sensor might be dirty. Clean it gently. If cleaning does not help, the sensor may need replacement. This ensures the boiler detects the flame properly.
E03 – High Limit Exceeded
This code appears when the boiler temperature is too high. Check the thermostat settings. Allow the boiler to cool down. If the problem continues, the thermostat might be faulty.
E04 – Low Water Pressure
Low water pressure can stop the boiler. Refill the system to the correct level. Check for leaks in the system. Repair any leaks to prevent pressure drops.
E05 – Sensor Error
This indicates a sensor malfunction. Inspect the sensors. Replace any faulty ones. Proper sensor function is crucial for safe operation.
Pilot Light Problems
Experiencing issues with the pilot light on your Laars Mini Therm Boiler can be frustrating. The pilot light is crucial for the proper functioning of the boiler. In this section, we will address common problems related to the pilot light. Understanding these issues can help you troubleshoot and fix your boiler efficiently.
Pilot Light Not Staying Lit
If your pilot light does not stay lit, there are several potential causes. Below are some common issues and solutions:
- Dirty Pilot Orifice: A dirty orifice can block gas flow. Clean the orifice with a small brush.
- Thermocouple Issues: A faulty thermocouple may not detect the flame. Replace the thermocouple if necessary.
- Insufficient Gas Supply: Ensure the gas valve is fully open. Check for any gas leaks.
- Drafts: Strong drafts can extinguish the pilot light. Shield the pilot light area from wind.
Ignition Failure
When the pilot light fails to ignite, it can be due to several reasons. Here are some common culprits and their fixes:
- Igniter Malfunction: The igniter may be dirty or faulty. Clean or replace the igniter.
- Gas Valve Issues: The gas valve might be stuck or damaged. Inspect and replace the gas valve if needed.
- Air in Gas Line: Air in the gas line can prevent ignition. Bleed the gas line to remove air.
- Electrical Problems: Check the electrical connections. Ensure they are secure and functional.
For easier reference, here is a summary table of common pilot light problems and their solutions:
Problem | Solution |
---|---|
Dirty Pilot Orifice | Clean the orifice with a small brush |
Faulty Thermocouple | Replace the thermocouple |
Insufficient Gas Supply | Ensure the gas valve is fully open |
Strong Drafts | Shield the pilot light area from wind |
Igniter Malfunction | Clean or replace the igniter |
Gas Valve Issues | Inspect and replace the gas valve |
Air in Gas Line | Bleed the gas line |
Electrical Problems | Check and secure electrical connections |
Understanding these common pilot light problems can help you diagnose and fix your Laars Mini Therm Boiler. Regular maintenance can prevent many of these issues, ensuring your boiler runs smoothly.
Thermostat Issues
Thermostat issues can disrupt the efficiency of your Laars Mini Therm Boiler. It is crucial to address these problems promptly to maintain optimal performance. Understanding common thermostat issues can help you troubleshoot and fix them.
Incorrect Temperature Readings
One common thermostat issue is incorrect temperature readings. This can cause your boiler to work harder than necessary. Check if the thermostat is placed near heat sources. This can lead to false readings. If the thermostat is not calibrated correctly, it can also show incorrect temperatures. Ensure it is set up properly and away from direct sunlight or other heat sources.
Thermostat Not Responding
Another frequent problem is the thermostat not responding. This could be due to dead batteries. Replace the batteries and see if it starts working. If the thermostat is still unresponsive, check the wiring connections. Loose or damaged wires can cause a lack of response. Make sure all connections are secure.
If the issue persists, the thermostat might need a reset. Refer to the user manual for reset instructions. Sometimes, a simple reset can fix the problem. If none of these solutions work, it might be time to replace the thermostat.
Water Leaks
Water leaks in a Laars Mini Therm Boiler can cause many problems. Leaks can affect the boiler’s efficiency and potentially damage your home. Properly identifying and fixing leaks is crucial to maintain your system’s performance.
Identifying Leaks
Spotting leaks early can prevent bigger issues. Here are some signs:
- Puddles of water around the boiler
- Damp spots on walls or floors
- Rust on pipes or boiler parts
- Low water pressure in the system
If you see these signs, inspect the boiler closely. Check all connections, valves, and seals. Look for any signs of water droplets or moisture.
Fixing Leaks
Fixing a leak depends on its source. Here are common methods:
- Replace Seals and Gaskets: Worn seals can cause leaks. Replace them to stop the leak.
- Tighten Connections: Loose connections may lead to leaks. Use a wrench to tighten any loose fittings.
- Patch Small Holes: Small holes in pipes can be patched with epoxy putty. Apply it to the hole and let it cure.
- Replace Damaged Parts: Severely damaged parts might need replacement. Consult your boiler’s manual for part numbers and instructions.
If the leak persists after these steps, contact a professional technician. They have the tools and knowledge to handle complex issues.
Noisy Boiler
Experiencing a noisy boiler can be quite unsettling. Laars Mini Therm boilers, known for their reliability, can sometimes develop noise issues. Understanding the source of these sounds can help you address the problem effectively. Let’s explore the common noises and their causes.
Banging Sounds
Banging sounds in your Laars Mini Therm boiler can be alarming. This noise often indicates trapped air within the system. Bleeding the radiators can usually resolve this. Another cause could be low water pressure. Check the pressure gauge and adjust as needed. Sediment buildup in the boiler can also cause banging sounds. Flushing the system may help. If the issue persists, consult a professional.
Whistling Noises
Whistling noises often point to a different problem. These sounds usually occur due to a buildup of limescale. This is common in areas with hard water. A descaling solution can help clear the limescale. Another possible cause is a worn-out pump. The pump may need replacement to stop the whistling. Incorrectly set thermostat settings can also lead to whistling. Ensure the thermostat is set correctly. If none of these solutions work, seek expert advice.
Maintenance Tips
Regular maintenance of your Laars Mini Therm Boiler ensures efficient operation and long-term reliability. Proper care can prevent unexpected breakdowns and expensive repairs. Follow these maintenance tips for the best performance.
Regular Inspections
Frequent inspections help catch potential issues early. Check for any leaks or corrosion around the boiler. Look for unusual noises or vibrations, as these can be signs of problems.
Create a simple inspection checklist:
- Examine the pilot light for a steady blue flame.
- Check for water leaks around the boiler.
- Inspect the pressure gauge to ensure it’s within the normal range.
- Listen for unusual noises from the boiler.
Cleaning Components
Cleaning is crucial for maintaining boiler efficiency. Dust and debris can cause blockages and reduce performance. Keep the following components clean:
Component | Cleaning Frequency |
---|---|
Burner Assembly | Every 6 months |
Heat Exchanger | Annually |
Air Vents | Quarterly |
Use a soft brush to remove dirt from the burner assembly. Clean the heat exchanger with a vacuum to remove soot. Ensure air vents are clear to maintain proper airflow.
Following these maintenance tips can significantly extend the life of your Laars Mini Therm Boiler. Regular inspections and cleaning are essential for optimal operation.
When To Call A Professional
When dealing with a Laars Mini Therm Boiler, knowing when to call a professional can save you time and money. Some problems require immediate expert intervention. Routine maintenance also benefits from professional oversight. Understanding the difference ensures your boiler remains efficient and safe.
Severe Issues
Severe issues with your Laars Mini Therm Boiler need a professional’s touch. If you experience frequent boiler shutdowns, it could signal a major problem. Professionals have the tools to diagnose and fix such issues.
Unusual noises coming from your boiler also require expert attention. Strange sounds often indicate internal problems. Addressing them early prevents further damage.
Water leaks around your boiler pose a serious risk. Leaks can damage your home and the boiler itself. A professional can identify the source and stop the leak effectively.
Gas odors around your boiler are dangerous. Gas leaks can lead to serious accidents. Always call a professional immediately if you smell gas.
Routine Maintenance
Routine maintenance keeps your Laars Mini Therm Boiler running smoothly. Professionals perform thorough checks that ensure optimal performance.
Regular cleaning of the boiler components is vital. Dust and debris can hinder efficiency. A professional can clean these parts safely.
Periodic inspections by a professional help identify potential issues early. Early detection can save you from costly repairs in the future.
Professionals also check system pressure and make adjustments. Proper pressure levels are crucial for efficient operation.
Finally, professional maintenance includes testing safety controls. Ensuring these controls work correctly is vital for your safety.
Frequently Asked Questions
Why Is My Laars Mini Therm Boiler Not Heating?
Your boiler may not heat due to thermostat issues, low water pressure, or pilot light problems.
How Do I Reset My Laars Mini Therm Boiler?
Find the reset button on your boiler. Press and hold it for 10 seconds.
What Should I Do If My Boiler Is Leaking?
Turn off the water supply. Call a professional to inspect and repair the leak.
Why Is My Boiler Making Unusual Noises?
Noises often indicate air in the system, low water pressure, or a malfunctioning pump.
How Often Should I Service My Laars Mini Therm Boiler?
Service your boiler annually. Regular maintenance ensures efficiency and prevents breakdowns.
Conclusion
Troubleshooting your Laars Mini Therm Boiler can be straightforward. Follow the steps mentioned earlier in the blog. Regular maintenance helps prevent most issues. Always ensure safety when handling the boiler. Seek professional help if problems persist. A well-maintained boiler ensures efficient heating.
Keep your home warm and comfortable. Stay proactive with boiler care. This saves time and money in the long run. Happy heating!