Porter Cable air compressors are reliable tools. But like any machine, they can have issues.
Experiencing problems with your Porter Cable air compressor can be frustrating, especially when you need it most. Whether it’s a lack of pressure, strange noises, or the unit not starting at all, troubleshooting is essential. This guide will help you identify and solve common issues with your Porter Cable air compressor.
With a little patience and the right approach, you can get your air compressor back to working condition quickly. Read on to understand the common problems and their solutions, ensuring your tool stays in top shape.
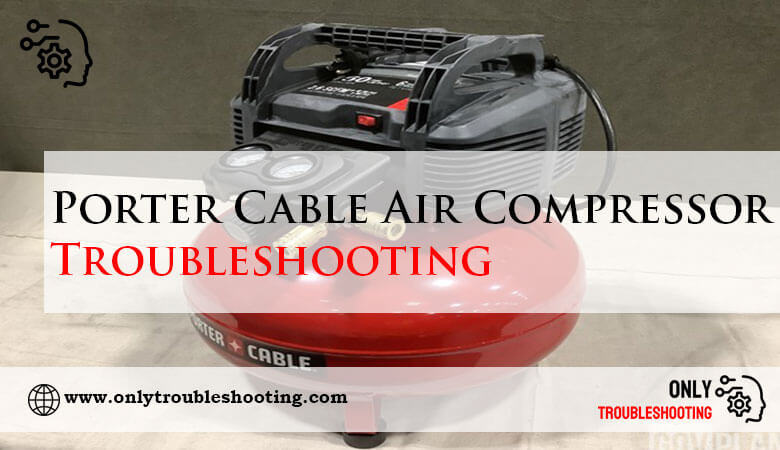
Credit: onlytroubleshooting.com
Common Issues
Porter Cable air compressors are reliable and efficient tools. But, like any machine, they can have problems. Understanding common issues can help you fix them quickly. Below are some frequent problems and how to address them.
No Power
One common issue is the compressor not powering on. First, check if it is plugged in. Sometimes, the cord can come loose. Next, inspect the fuse or circuit breaker. Reset it if needed. If it still won’t start, the power switch might be faulty. You may need to replace it. Always ensure the power source is functional.
Low Pressure
Low pressure is another frequent problem. Check the air filter first. A dirty filter can reduce air flow. Clean or replace it if needed. Inspect the hoses for leaks. Even a small leak can cause low pressure. Tighten any loose connections. If the pressure is still low, the regulator might be faulty. Adjust or replace it as required.
Overheating
Overheating can damage the compressor. Ensure the unit is in a well-ventilated area. Poor airflow can cause it to overheat. Check the cooling fans. They should be clean and operational. If the compressor runs continuously, let it rest. Overuse can lead to overheating. Regular maintenance helps prevent this issue.
Preliminary Checks
Ensuring your Porter Cable Air Compressor functions properly involves a few key preliminary checks. These checks can prevent common issues and save time. Start with these three essential areas.
Power Source
First, inspect the power source. Confirm the power outlet is working. Use a multimeter to check the voltage. The compressor needs a consistent power supply.
Make sure the outlet matches the compressor’s voltage requirement. If the outlet is faulty, fix or replace it. A steady power source ensures your compressor runs smoothly.
Circuit Breaker
Next, verify the circuit breaker. A tripped circuit breaker can stop the compressor. Locate the breaker box and see if the breaker is in the “off” position.
If tripped, reset it by flipping it back to the “on” position. Check for any signs of electrical overload. A functioning circuit breaker is crucial for compressor operation.
Extension Cord
Lastly, examine the extension cord. Avoid using a long or thin extension cord. It can cause voltage drops and overheating.
Opt for a heavy-duty extension cord designed for high-power tools. Ensure the cord is free from cuts and damage. A proper extension cord maintains the power flow to your compressor.
Check | Action |
---|---|
Power Source | Verify outlet voltage |
Circuit Breaker | Reset if tripped |
Extension Cord | Use heavy-duty cord |
Inspecting Components
To keep your Porter Cable air compressor running smoothly, regular inspections are essential. By checking its components, you can identify and fix issues early. This will help in avoiding costly repairs and downtime. Let’s explore the key parts to inspect.
Air Filter
The air filter is crucial for clean air intake. A dirty air filter can reduce performance. Check the air filter for dirt and debris. If it’s clogged, clean or replace it. This simple step can boost the compressor’s efficiency.
Pressure Switch
The pressure switch controls the compressor’s on and off cycle. Inspect the switch for any signs of wear. Ensure it responds properly to pressure changes. If it’s faulty, the compressor might not start or stop correctly. Replace the switch if needed to maintain optimal function.
Regulator
The regulator adjusts the air pressure delivered to your tools. Examine the regulator for leaks or damage. Make sure it sets and holds the desired pressure accurately. If the regulator is malfunctioning, replace it to ensure consistent performance.
Fixing Air Leaks
Fixing air leaks in your Porter Cable air compressor can save you time and money. Air leaks reduce efficiency and can cause the compressor to overwork. By identifying and fixing air leaks, you ensure your compressor works at its best.
Hose Connections
Check all hose connections for any signs of wear or damage. Loose or damaged connections can cause air leaks. Tighten or replace any faulty hoses to prevent leaks. Ensure the hoses are securely attached to the compressor.
Fittings
Inspect the fittings for any cracks or damages. Use soapy water to detect leaks. Apply the soapy water to the fittings and watch for bubbles. Bubbles indicate a leak. Replace or tighten the fittings as needed to stop the leaks.
Tank Drain Valve
The tank drain valve can also be a source of air leaks. Check if the valve is tightly closed. If it is loose or damaged, it can cause air to escape. Replace the valve if necessary to ensure a proper seal.
Maintenance Tips
Maintaining your Porter Cable air compressor ensures it runs smoothly and lasts longer. Regular upkeep can prevent issues and save you from costly repairs. Follow these maintenance tips to keep your air compressor in top shape.
Regular Cleaning
Keeping the air compressor clean is essential. Dirt and debris can cause malfunctions. Here are some steps for regular cleaning:
- Unplug the compressor before cleaning.
- Use a damp cloth to wipe down the exterior.
- Clean the air intake vents with a brush.
- Ensure the compressor is dry before plugging it back in.
Oil Levels
Oil is crucial for the air compressor’s performance. Check and maintain the oil levels regularly. Follow these steps:
- Place the compressor on a level surface.
- Locate the oil sight glass or dipstick.
- Check the oil level against the recommended mark.
- Add oil if needed, using the recommended type.
- Do not overfill the oil.
Proper oil levels ensure smooth operation and prevent damage.
Filter Replacement
The air filter keeps dust and debris out of the compressor. A clean filter is vital for performance. Replace the filter regularly:
Step | Description |
---|---|
1 | Turn off and unplug the compressor. |
2 | Locate the air filter housing. |
3 | Remove the old filter. |
4 | Install a new filter. |
5 | Secure the filter housing. |
Replacing the filter ensures clean air intake and optimal performance.
Following these maintenance tips helps your Porter Cable air compressor function efficiently. Regular cleaning, checking oil levels, and replacing filters are simple yet effective steps.
Advanced Troubleshooting
Advanced troubleshooting for a Porter Cable air compressor can save you time and money. Understanding and fixing the common issues helps maintain the compressor’s efficiency. Below are some advanced troubleshooting tips for motor issues, valve problems, and pump failures.
Motor Issues
The motor is the heart of the air compressor. If it fails to start, check the power supply first. Ensure the compressor is plugged into a working outlet. Inspect the cord for any damage. A broken cord can prevent the motor from receiving power.
If the motor runs but the compressor does not build pressure, check the belt. A loose or damaged belt can cause this issue. Tighten or replace the belt as needed. Also, inspect the capacitor. A faulty capacitor can cause the motor to malfunction. Replace it if necessary.
Valve Problems
Valves regulate the air flow within the compressor. If the compressor does not build or hold pressure, the valves might be the issue. Listen for hissing sounds, indicating a valve leak. To fix it, disassemble the valve and clean it. Sometimes, debris can block the valve, causing it to malfunction.
Check the intake and exhaust valves. If they are worn or damaged, replace them. Ensure that the valves are properly seated. Misaligned valves can also cause pressure problems.
Pump Failures
The pump is crucial for air compression. If the pump fails, the compressor will not work correctly. First, check the oil level. Low oil can cause the pump to overheat and fail. Add oil if necessary.
Inspect the pump’s pistons and cylinders. Worn-out parts can cause the pump to lose efficiency. Replace any damaged components. Also, check for air leaks in the pump. Tighten all connections to ensure there are no leaks.
Regular maintenance can prevent pump failures. Clean the air filter regularly and ensure all parts are lubricated. Proper care extends the life of the pump.
Safety Precautions
Ensuring safety is crucial when troubleshooting your Porter Cable air compressor. Follow these safety precautions to avoid accidents and injuries. Below are the key areas you should focus on:
Protective Gear
Always wear the right protective gear when handling air compressors. This includes:
- Safety goggles to protect your eyes from debris and dust.
- Hearing protection like earplugs or earmuffs to prevent hearing loss.
- Gloves to protect your hands from sharp objects and hot surfaces.
Wearing this gear reduces the risk of injury.
Proper Ventilation
Ensure your workspace has proper ventilation to avoid inhaling harmful fumes. Air compressors can release toxic gases. To ensure safety:
- Work in an open area or a well-ventilated room.
- Use exhaust fans to improve air circulation.
- Avoid using the compressor in confined spaces.
These steps help maintain a safe breathing environment.
Regular Inspections
Conduct regular inspections on your air compressor to ensure it operates safely. Check for:
- Leaking hoses and connections.
- Worn-out parts or accessories.
- Proper oil levels and cleanliness.
Regular checks help identify issues early and prevent accidents.
By following these safety precautions, you can troubleshoot your Porter Cable air compressor effectively and safely.
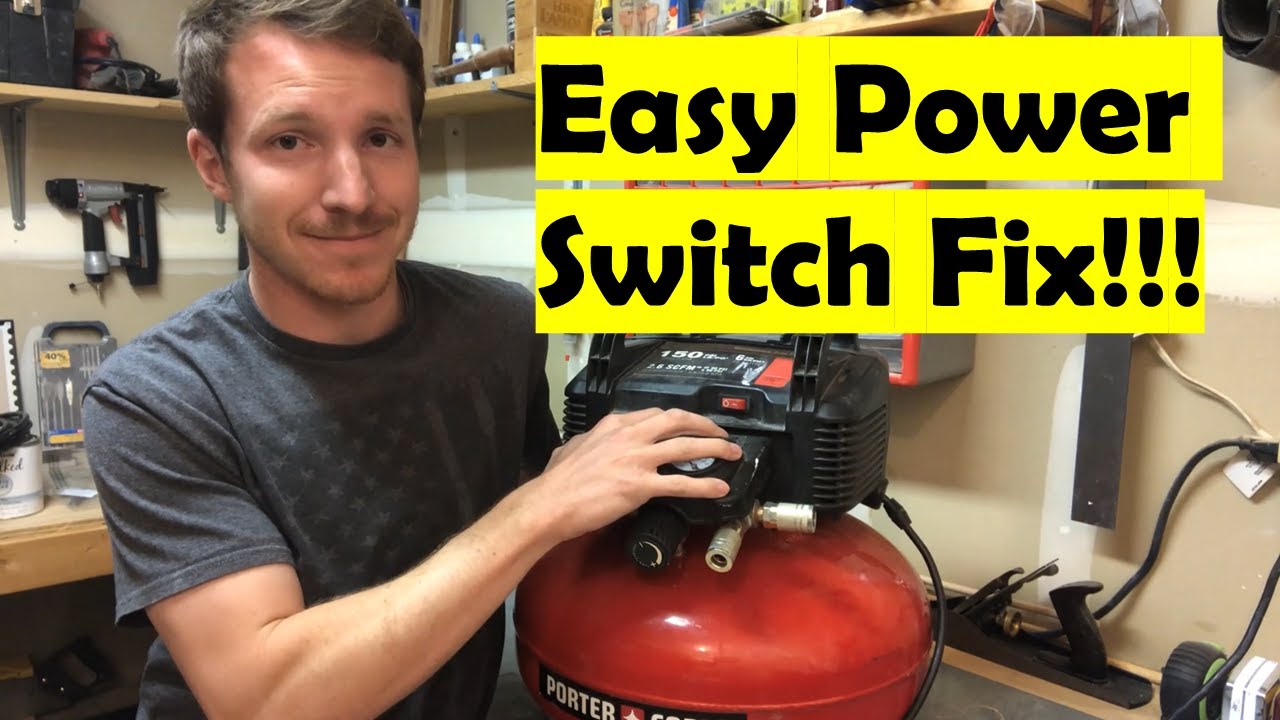
Credit: m.youtube.com
When To Seek Professional Help
Porter Cable air compressors are reliable machines. Yet, they can face issues. Sometimes, you can fix these problems on your own. But there are times when seeking professional help is best. This section will guide you on when to call an expert.
Recurring Problems
If your air compressor shows the same issue repeatedly, it may need professional attention. Recurring problems can indicate deeper issues. For example:
- Frequent start-up failures
- Constantly tripping circuit breakers
- Persistent leaks
These signs often point to underlying faults. An expert can identify and fix these problems effectively.
Complex Repairs
Some repairs are too complex for DIY fixes. If your compressor needs complex repairs, consider professional help. Examples include:
- Motor replacements
- Internal part failures
- Electrical issues
Attempting these repairs without expertise can be risky. It may cause further damage. Professionals have the right tools and knowledge to handle these repairs safely.
Warranty Concerns
If your air compressor is under warranty, avoid doing repairs yourself. Warranty concerns are crucial. Doing DIY repairs can void your warranty. Instead, check your warranty terms. Often, they require professional service for repairs. This ensures:
- Proper handling of your machine
- Maintaining warranty coverage
- Long-lasting repairs
Always contact the authorized service center for any warranty-related repairs. This protects your investment and ensures quality service.

Credit: m.youtube.com
Frequently Asked Questions
Why Is My Porter Cable Air Compressor Not Starting?
Check the power source and ensure the plug is secure. Also, inspect the circuit breaker.
How Do I Fix A Leaking Air Compressor?
Tighten all connections and replace any damaged seals or hoses. Inspect for cracks.
Why Does My Air Compressor Keep Shutting Off?
The motor could be overheating. Clean or replace the air filter. Check for proper ventilation.
How Do I Increase The Pressure On My Air Compressor?
Adjust the pressure regulator knob. Refer to the user manual for specific instructions.
What Maintenance Does My Air Compressor Need?
Regularly drain the tank, change the oil, and clean filters. Inspect for wear and tear.
Conclusion
Troubleshooting your Porter Cable air compressor can be straightforward. Follow the steps outlined. Ensure regular maintenance for a longer lifespan. Check connections and replace worn parts promptly. Always keep the user manual handy. This helps in quick fixes and understanding the machine.
With these tips, your compressor will work efficiently. Avoid frustration and save money on repairs. Happy troubleshooting!