Scotsman ice machines are known for their reliability and efficiency. But even the best machines can sometimes have issues.
If your Scotsman ice machine isn’t working right, don’t worry. Many common problems have simple solutions. This guide will help you identify and fix typical issues. From no ice production to strange noises, we cover it all. Clear, step-by-step instructions will make troubleshooting easy.
Whether you’re a novice or have some experience, this guide is for you. Let’s get your Scotsman ice machine back to peak performance quickly and easily.
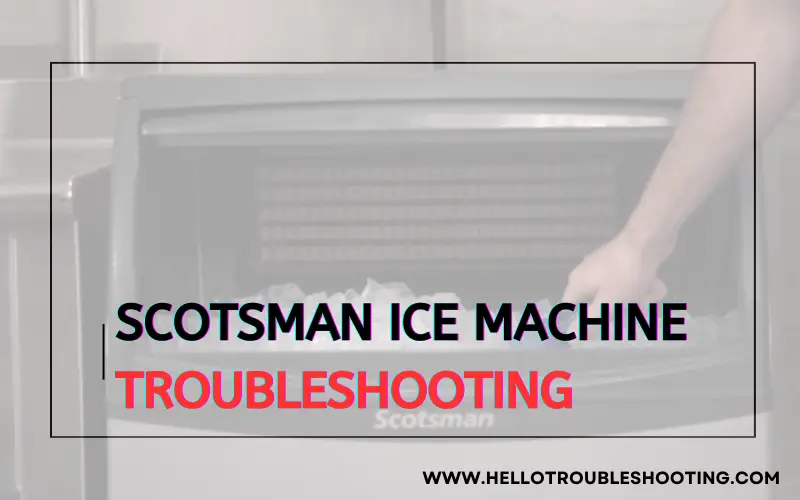
Introduction To Scotsman Ice Machines
Scotsman Ice Machines are known for their durability and efficiency. They are popular in various industries. Understanding how they work and troubleshooting them can save time and money.
History And Features
Scotsman Ice Machines have a long history. They began in the 1950s. The company was founded to provide reliable ice machines. Over the years, they have improved their technology. Today, Scotsman Ice Machines offer many features:
- Energy efficiency: Uses less power, saving on electricity bills.
- Self-cleaning: Reduces maintenance time and effort.
- Various ice types: Cubes, flakes, and nuggets to suit different needs.
- Durability: Built to last with high-quality materials.
Importance In Various Industries
Scotsman Ice Machines are essential in many industries. They are used in:
- Restaurants: Keeps drinks cold and fresh for customers.
- Healthcare: Provides clean ice for medical use.
- Hotels: Ensures guests have ice for their drinks.
- Convenience stores: Offers bagged ice for sale.
These machines ensure smooth operations in various settings. They help maintain quality and hygiene standards.
Common Issues Faced
Scotsman ice machines are known for their reliability and performance. Yet, like any machinery, they can face issues. Understanding these common problems can help you troubleshoot effectively. Below are some frequent issues you may encounter.
No Ice Production
If your Scotsman ice machine is not producing ice, there could be several reasons. First, check if the machine is plugged in and turned on. Ensure the water supply is connected and the valve is open. A clogged water filter can also stop ice production. Replace the filter if it hasn’t been changed in a while. Finally, inspect the machine for any signs of damage or wear.
Slow Ice Production
Slow ice production can be frustrating. Check the ambient temperature around the machine. High temperatures can slow down ice making. Clean the condenser coils to improve efficiency. Ensure the water supply is not restricted. A low water flow can slow production. Regular maintenance can prevent slow ice production.
Poor Ice Quality
Poor ice quality can affect your business. Cloudy or misshapen ice can be unappealing. Start by checking the water quality. Hard water can cause poor ice quality. Install a water softener if needed. Clean the ice machine regularly to prevent mineral buildup. Replace old or worn-out parts that may affect ice quality.
Basic Maintenance Tips
Keeping your Scotsman ice machine running smoothly requires regular maintenance. Simple tasks can prevent bigger issues and ensure efficient operation. Follow these basic maintenance tips to keep your ice machine in top shape.
Regular Cleaning
Regular cleaning is crucial for your Scotsman ice machine. Dirt and debris can clog the system and reduce efficiency. Clean the machine at least once a month.
- Unplug the machine before cleaning.
- Use a soft cloth and mild detergent.
- Wipe down the exterior and interior surfaces.
- Rinse with water and let it dry completely.
Checking Filters
Filters play a significant role in the smooth operation of your ice machine. Dirty filters can block water flow and affect ice quality. Check the filters every two weeks.
- Locate the filters in your machine.
- Remove the filters carefully.
- Rinse them under running water.
- Reinstall the filters once they are dry.
Inspecting Water Supply
The water supply is essential for ice production. Insufficient water can lead to smaller ice cubes or no ice at all. Inspect the water supply regularly.
Inspection Task | Frequency |
---|---|
Check water lines for leaks | Weekly |
Ensure water pressure is adequate | Monthly |
Inspect water inlet valve | Monthly |
If you find any issues with the water supply, address them immediately. Ensuring a steady water flow will keep your ice machine working efficiently.
Troubleshooting No Ice Production
Is your Scotsman ice machine not producing ice? This issue can stem from various causes. Identifying the root of the problem is crucial. Let’s explore some common reasons behind no ice production and how to troubleshoot them.
Power Supply Check
First, ensure the machine is getting power. A faulty power supply can stop ice production. Here’s how to check:
- Inspect the power cord for any damage.
- Confirm the machine is plugged into a working outlet.
- Check the circuit breaker. It should not be tripped.
If everything seems fine, use a multimeter to test the outlet’s voltage. The reading should match the machine’s requirements. If not, call an electrician.
Water Supply Issues
Water supply problems can also halt ice production. Follow these steps to check:
- Ensure the water valve is open.
- Examine the water line for any kinks or blockages.
- Clean the water filter if it’s clogged.
If the water supply is interrupted, the ice machine cannot produce ice. Regular maintenance can prevent these issues.
Thermostat Problems
The thermostat controls the ice-making process. If it malfunctions, the machine won’t produce ice. Here’s what to do:
- Check the thermostat settings. They should be at the recommended temperature.
- Listen for a clicking sound when adjusting the thermostat. No sound means it might be broken.
- Consider replacing the thermostat if it’s faulty.
A malfunctioning thermostat needs attention. Replacing it can often resolve the issue.
By following these steps, you can troubleshoot your Scotsman ice machine effectively. Keep your machine well-maintained to avoid future problems.
Addressing Slow Ice Production
Slow ice production can be frustrating for any business. Ensuring your Scotsman ice machine runs efficiently is crucial. Let’s explore some common solutions to speed up ice production.
Temperature Adjustments
Temperature plays a critical role in ice production. Check the room temperature. Ensure it stays between 55°F and 90°F. Extreme temperatures can hinder ice creation. Adjust the thermostat if necessary. A consistent temperature helps the machine function properly.
Cleaning Condenser Coils
Dirty condenser coils can slow ice production. Regular cleaning is essential. Follow these steps:
- Turn off the ice machine.
- Locate the condenser coils.
- Use a soft brush or vacuum to remove debris.
- Wipe the coils with a damp cloth.
- Turn the machine back on.
Clean coils ensure better air flow. This leads to more efficient ice production.
Inspecting Evaporator
The evaporator must be in good condition. Inspect it regularly. Look for signs of wear or damage. Common issues include:
- Ice build-up
- Corrosion
- Leaks
If you find any problems, address them immediately. A well-maintained evaporator is key to fast ice production.
Improving Ice Quality
Ensuring the ice quality of your Scotsman Ice Machine is crucial. It guarantees customer satisfaction and maintains the machine’s efficiency. This section will cover three essential steps to improve ice quality. These steps include water filtration, adjusting the freezing cycle, and cleaning the ice bin.
Water Filtration
Water filtration plays a vital role in producing clear, high-quality ice. A good filter removes impurities, minerals, and chlorine. This prevents cloudy ice and bad taste. To enhance your ice quality, ensure you:
- Install a high-quality water filter.
- Replace the filter regularly, as per the manufacturer’s guidelines.
- Check for any leaks or damage in the filter system.
Using a reliable water filter enhances ice clarity and taste. It also extends the life of your Scotsman Ice Machine.
Adjusting Freezing Cycle
Adjusting the freezing cycle can significantly impact ice quality. The freezing cycle determines how long water freezes to form ice. Follow these steps to adjust the freezing cycle:
- Refer to the user manual for cycle settings.
- Adjust the cycle time as needed to optimize ice hardness and clarity.
- Monitor ice production after adjustments.
Properly adjusted freezing cycles result in clearer, harder ice. This enhances the overall customer experience.
Cleaning Ice Bin
A clean ice bin is essential for maintaining ice quality. Dirt, mold, or bacteria can affect the taste and safety of the ice. Regular cleaning of the ice bin is necessary:
- Empty the ice bin completely.
- Use a mild detergent and warm water to clean the bin.
- Rinse thoroughly to remove any soap residue.
- Dry the bin completely before refilling it with ice.
Keeping the ice bin clean ensures that your ice remains fresh and safe. It also prevents unpleasant odors and tastes.
Advanced Troubleshooting Techniques
Advanced troubleshooting techniques can help keep your Scotsman ice machine running smoothly. These methods are ideal for resolving complex issues. This section covers diagnosing electrical problems, replacing faulty parts, and when to seek professional help.
Diagnosing Electrical Issues
Electrical issues can cause your Scotsman ice machine to malfunction. Start by checking the power supply. Ensure the machine is plugged in properly. Also, check the circuit breaker.
Next, use a multimeter to test the power outlet. Ensure it delivers the correct voltage. Inspect the machine’s wiring for any visible damage. Look for frayed or exposed wires. Replace damaged wires immediately.
Check the control board for any signs of burns or corrosion. Faulty control boards can disrupt the machine’s operation. If the board looks damaged, it may need replacement. Always follow safety guidelines when working with electrical components.
Replacing Faulty Parts
Sometimes, replacing faulty parts can fix your ice machine. Identify the malfunctioning part first. Common parts that may need replacement include:
- Thermostats
- Water pumps
- Solenoid valves
- Compressors
Refer to the machine’s manual for part specifications. Purchase the correct replacement parts. Use the right tools for installation. For example, a screwdriver, pliers, or wrench might be needed.
Follow the step-by-step instructions in the manual. If unsure, consult a professional for assistance. Proper installation ensures the machine works efficiently.
Professional Assistance
Some issues may require professional help. For complex electrical problems, contact a licensed technician. They have the expertise to safely handle high-voltage components.
If the machine is under warranty, reach out to the manufacturer. They can provide authorized service technicians. This ensures quality repairs.
Regular maintenance by professionals can prevent future issues. Schedule routine check-ups to keep your ice machine in optimal condition. Professional assistance guarantees safe and efficient operation.
When To Call A Professional
Knowing when to call a professional for your Scotsman ice machine troubleshooting can save you time and money. While some issues can be resolved with basic troubleshooting, others require the expertise of a skilled technician. Below, we will discuss key factors to consider before making that call.
Recognizing Complex Problems
Some issues are too complex for a quick fix. If your ice machine has electrical issues or internal leaks, it’s time to call a professional. Other signs include:
- Persistent error codes
- Unusual noises
- Water supply problems
These problems often indicate deeper issues that need professional attention.
Cost-benefit Analysis
Before calling a technician, consider the cost-benefit analysis. Sometimes, the cost of professional repair is high. Compare it with the cost of a new machine.
Issue | Repair Cost | Replacement Cost |
---|---|---|
Minor Electrical Issues | $100-$200 | $2000+ |
Water Supply Problems | $150-$300 | $2000+ |
Internal Leaks | $200-$500 | $2000+ |
If repair costs are high, replacing the machine may be more cost-effective.
Finding A Reliable Technician
Finding a reliable technician is crucial. Look for these qualities:
- Certified and licensed
- Good reviews
- Experience with Scotsman ice machines
You can also ask for recommendations from friends or read online reviews to make a well-informed choice.
Preventive Measures
Scotsman Ice Machines are reliable, but they need regular care. Taking preventive measures can extend their lifespan and enhance performance. Here are some effective steps you can follow.
Routine Inspections
Conducting routine inspections is crucial. Check for any visible damage or wear. Look for leaks, strange noises, and irregular ice production. Inspect the water supply and drainage systems. These simple steps can help spot issues early.
Scheduled Maintenance
Regular maintenance ensures your machine runs smoothly. Create a maintenance schedule. Follow the manufacturer’s guidelines. Clean the ice machine regularly. Use approved cleaning solutions. Replace the water filter as recommended. These actions prevent buildup and contamination.
Upgrading Components
Sometimes, you need to upgrade components. Replace old or worn-out parts. Consider using newer, more efficient parts. This can improve the performance and longevity of your ice machine. Upgrading components can also reduce energy consumption.
Component | Upgrade Benefit |
---|---|
Water Filter | Improves water quality, enhances ice taste |
Condensers | Boosts efficiency, reduces energy use |
Fans | Ensures better cooling, prolongs lifespan |
By following these preventive measures, you ensure your Scotsman Ice Machine remains in top condition. Routine inspections, scheduled maintenance, and upgrading components can make a huge difference. Stay proactive and enjoy continuous, high-quality ice production.

Frequently Asked Questions
Why Is My Scotsman Ice Machine Not Making Ice?
Your Scotsman ice machine might not be making ice due to a clogged filter, low water pressure, or a malfunctioning component. Check the water supply and filters first.
How Do I Reset My Scotsman Ice Machine?
To reset your Scotsman ice machine, locate the reset button on the control panel, press, and hold it for a few seconds until the machine restarts.
What Causes A Scotsman Ice Machine To Freeze Up?
A Scotsman ice machine can freeze up due to improper airflow, dirty condenser coils, or incorrect temperature settings. Ensure proper ventilation and clean the coils regularly.
How Often Should I Clean My Scotsman Ice Machine?
You should clean your Scotsman ice machine every six months. Regular cleaning prevents buildup, ensures efficient operation, and maintains the quality of the ice.
Conclusion
Maintaining your Scotsman ice machine ensures it runs smoothly. Regular cleaning prevents issues. Addressing minor problems early can save money and hassle. Always consult your manual for guidance. If problems persist, contacting a professional may be necessary. Keeping your ice machine in top shape guarantees fresh ice.
Follow these troubleshooting tips to keep your Scotsman ice machine efficient. Reliable ice production is key for your needs. Stay proactive and enjoy trouble-free ice.