Follett Ice Machine Troubleshooting can save time and money. It’s essential to know common issues and solutions.
Ice machines are vital in many industries. Restaurants, hospitals, and offices rely on them daily. A malfunction can disrupt operations. Understanding how to troubleshoot your Follett ice machine can help. You can solve minor problems quickly. This guide covers common issues and fixes.
Learn about error codes, water supply problems, and maintenance tips. With this knowledge, you’ll keep your ice machine running smoothly. Avoid costly repairs and downtime. Ready to dive in? Let’s explore Follett Ice Machine Troubleshooting together.

Credit: www.youtube.com
Common Ice Machine Issues
Understanding the common issues with Follett ice machines can save you time and money. This guide will help you troubleshoot common problems like no ice production and slow ice production.
No Ice Production
When your Follett ice machine stops making ice, it can be frustrating. Here are some possible causes and solutions:
- Power Issues: Ensure the machine is plugged in and turned on. Check the circuit breaker.
- Water Supply: Verify the water supply line is open and not kinked. Inspect the water filter for clogs.
- Ice Bin Full: Some machines stop making ice when the bin is full. Empty the bin if needed.
- Temperature: Ensure the room temperature is within the recommended range. Extreme temperatures can affect ice production.
Slow Ice Production
Slow ice production can be due to various reasons. Here are a few to consider:
- Dirty Condenser Coils: Clean the condenser coils regularly. Dust and dirt can reduce efficiency.
- Low Water Pressure: Check the water pressure. Low pressure can slow down ice production.
- Incorrect Temperature: Ensure the machine is in a cool, well-ventilated area. High temperatures can slow ice-making.
- Scale Build-Up: Regularly descale the machine. Mineral deposits can hinder ice production.
By addressing these common issues, you can ensure your Follett ice machine runs smoothly and efficiently.
Power Problems
One of the most common issues with Follett Ice Machines is power problems. These issues can cause your machine to stop working. Addressing power issues promptly can save you time and money.
Checking Power Supply
The first step in troubleshooting power problems is checking the power supply. Ensure the machine is plugged into a working outlet. You can test this by plugging another device into the same outlet. If the outlet is working, the problem may be with the machine.
Next, check the power cord for any visible damage. A damaged cord can prevent the machine from receiving power. Replace the cord if it is damaged.
Ensure the machine’s power switch is turned on. Sometimes, the switch might be accidentally turned off.
Resetting The Machine
If the power supply is fine, try resetting the machine. Many Follett Ice Machines have a reset button. Press and hold the reset button for a few seconds.
If your machine does not have a reset button, you can manually reset it. Unplug the machine from the power source. Wait for 10-15 minutes, then plug it back in.
After resetting, check if the machine powers on. If it still does not work, there may be a more serious issue.
Possible Power Problems | Solutions |
---|---|
Machine not plugged in | Plug the machine into a working outlet |
Damaged power cord | Replace the power cord |
Power switch off | Turn on the power switch |
Machine needs reset | Press reset button or unplug and replug |
Water Supply Issues
Dealing with water supply issues in your Follett ice machine can be frustrating. A consistent water supply is crucial for smooth operation. Identifying and solving common water supply problems can keep your machine running efficiently. Below, we cover essential steps to troubleshoot water supply issues.
Inspecting Water Lines
First, check the water lines for any visible damage. Look for cracks or leaks. Damaged lines can restrict water flow. This can affect the ice-making process.
- Turn off the water supply before inspection.
- Examine the entire length of the water line.
- If you find any damage, replace the water line immediately.
If the water line is in good condition, ensure it is not kinked or twisted. A kinked line can reduce water flow, leading to issues with your ice machine.
Cleaning Water Filters
Water filters play a vital role in maintaining water quality. Over time, filters can become clogged with debris. This can reduce water flow and affect ice production.
- Locate the water filter in your Follett ice machine.
- Turn off the water supply to the machine.
- Remove the filter and inspect it for clogs or debris.
- If the filter is dirty, clean it thoroughly.
- Reinstall the filter and turn the water supply back on.
Regular filter cleaning ensures optimal water flow and quality. This helps your ice machine perform better.
Temperature Concerns
Temperature concerns are a common issue with Follett ice machines. Keeping the right temperature ensures the machine works efficiently. This section will guide you through adjusting the thermostat and checking the ambient temperature.
Adjusting Thermostat
The thermostat controls the temperature inside the ice machine. Adjusting it can solve many temperature-related problems.
Follow these steps to adjust the thermostat:
- Locate the thermostat inside the machine.
- Turn the thermostat knob to the desired setting.
- Wait for a few hours to see if the ice production improves.
If adjusting the thermostat does not help, the thermostat might be faulty. Consider consulting a professional for further assistance.
Checking Ambient Temperature
The ambient temperature around the ice machine affects its performance. Ensure the machine is in a suitable environment.
Here are some tips for checking the ambient temperature:
- Use a thermometer to measure the temperature around the machine.
- Ensure the room temperature is between 50°F and 90°F.
- Avoid placing the machine near heat sources like ovens or direct sunlight.
If the ambient temperature is too high or too low, adjust the machine’s location. A stable environment helps the machine work properly.
Important: Regularly check the temperature settings to ensure optimal ice production.
Ice Quality Problems
Ice quality problems can be frustrating for any business. Follett ice machines are known for their reliability, but they are not without issues. Addressing these problems quickly ensures your ice supply remains consistent and clean. Below, we discuss common ice quality issues and how to troubleshoot them.
Cloudy Ice
Cloudy ice can be an eyesore and affect the taste of drinks. Several factors can cause cloudy ice in your Follett ice machine. Here’s a breakdown of common causes and solutions:
Cause | Solution |
---|---|
Water Impurities | Use a water filter to remove impurities. |
Air Trapped in Water | Ensure proper water flow and check for air leaks. |
Dirty Machine | Clean the machine regularly to prevent build-up. |
Misshapen Ice
Misshapen ice can affect the aesthetic and functionality of your ice. Here are common reasons for this issue and how to fix them:
- Incorrect Water Levels: Check and adjust the water level settings.
- Blocked Water Inlet: Ensure the water inlet is clear of obstructions.
- Temperature Fluctuations: Maintain a consistent ambient temperature around the machine.
Regular maintenance is key to preventing ice quality problems. Always follow the manufacturer’s guidelines for cleaning and upkeep. This ensures your Follett ice machine continues to produce high-quality ice.
Credit: www.follettice.com
Cleaning And Maintenance
Cleaning and maintenance are crucial for the optimal performance of your Follett ice machine. Regular cleaning ensures the machine runs efficiently and produces high-quality ice. Follow these steps to keep your machine in top shape.
Regular Cleaning Schedule
Maintaining a regular cleaning schedule is essential. Clean your Follett ice machine at least once a month. This schedule helps prevent the buildup of dirt and bacteria.
- Turn off the machine and unplug it.
- Remove all ice from the storage bin.
- Use a mild soap solution to clean the exterior.
- Rinse with clean water and dry with a soft cloth.
Regular cleaning keeps the machine hygienic and extends its lifespan.
Descaling Procedures
Descaling is vital for preventing mineral buildup. It should be done every 3-6 months.
- Prepare a descaling solution as per the manufacturer’s instructions.
- Pour the solution into the water reservoir.
- Run the machine until the reservoir is empty.
- Rinse the machine thoroughly with clean water.
Descaling improves the efficiency and quality of ice production.
Task | Frequency |
---|---|
Exterior Cleaning | Monthly |
Interior Cleaning | Monthly |
Descaling | Every 3-6 months |
Regular cleaning and descaling keep your Follett ice machine running smoothly. Clean machines produce better quality ice. Follow these steps to ensure optimal performance.
Error Codes And Diagnostics
Understanding error codes and diagnostics for your Follett ice machine is essential. It helps in identifying and fixing issues quickly. This guide will help you decode common error codes and run diagnostic tests effectively.
Interpreting Error Codes
Follett ice machines come with a built-in system to display error codes. These codes indicate different problems. Knowing what these codes mean can save you time and effort.
- E1: High water level. Check the water supply.
- E2: Low water level. Ensure the water valve is open.
- E3: Ice bin full. Empty the bin to continue ice production.
- E4: Temperature sensor fault. Inspect the sensor connection.
Running Diagnostic Tests
Running diagnostic tests on your Follett ice machine is straightforward. Follow these steps to ensure your machine runs smoothly:
- Press the “Menu” button on the control panel.
- Select the “Diagnostics” option using the arrow keys.
- Press “Enter” to start the diagnostic process.
- Wait for the machine to complete the tests. This may take a few minutes.
- Review the diagnostic results displayed on the screen.
Regular diagnostics can help you maintain your ice machine. It ensures the system is free from critical errors.
When To Call A Professional
Follett ice machines are reliable but can encounter issues. Knowing when to call a professional can save time and money. Attempting fixes without expertise may worsen the problem. This guide helps you decide when to seek expert help.
Identifying Major Issues
Major issues need professional attention. Here are some signs:
- Strange noises: Unusual sounds can signal mechanical problems.
- Water leakage: Leaks can cause damage and need urgent repair.
- Not making ice: If your machine stops making ice, it needs expert diagnosis.
- Electrical issues: Flickering lights or power problems are serious.
Finding A Qualified Technician
Choosing the right technician ensures your machine gets proper care. Follow these steps:
- Check credentials: Ensure the technician is certified and experienced.
- Read reviews: Customer reviews can provide insight into their service quality.
- Ask for references: Reliable technicians will provide references on request.
- Compare quotes: Get multiple quotes to ensure fair pricing.
For the best results, use a Follett-certified technician. They have specialized knowledge and access to genuine parts.
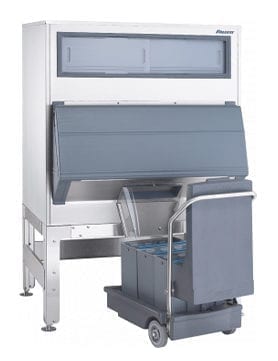
Credit: www.easyice.com
Frequently Asked Questions
How Do I Reset My Follett Ice Machine?
To reset your Follett ice machine, locate the reset button on the control panel. Press and hold it for a few seconds until the machine restarts.
Why Is My Follett Ice Machine Not Making Ice?
Your Follett ice machine might not make ice due to clogged filters, water supply issues, or faulty components. Check for blockages and ensure proper water flow.
How Often Should I Clean My Follett Ice Machine?
Clean your Follett ice machine every six months to maintain efficiency. Regular cleaning prevents buildup and ensures optimal performance. Follow the manufacturer’s guidelines for best results.
What Does The Red Light On My Follett Ice Machine Mean?
A red light on your Follett ice machine indicates an error or maintenance issue. Refer to the user manual for specific error codes and troubleshooting steps.
Conclusion
Troubleshooting your Follett ice machine can be simple with the right steps. Follow the guide to identify common issues and solutions. Regular maintenance ensures your machine runs smoothly. Clear any blockages and check for leaks. Always refer to the user manual for specific instructions.
If problems persist, consider seeking professional help. Keeping your ice machine in good condition will save time and money. Enjoy consistent ice production with proper care. Happy troubleshooting!