Taylor ice cream machines are known for their reliability and performance. But even the best machines can face issues.
Troubleshooting a Taylor ice cream machine can seem daunting, but it doesn’t have to be. Understanding common problems and their solutions is key to keeping your machine running smoothly. Ice cream machines are a crucial part of many businesses, serving up sweet treats to eager customers.
When your machine stops working, it impacts sales and customer satisfaction. Knowing how to troubleshoot can save time and money. In this guide, we’ll explore common issues you might encounter and offer practical solutions. Whether it’s a simple fix or a more complex problem, you’ll be better equipped to handle it. Let’s dive into the world of Taylor ice cream machine troubleshooting and keep those ice cream cones coming!
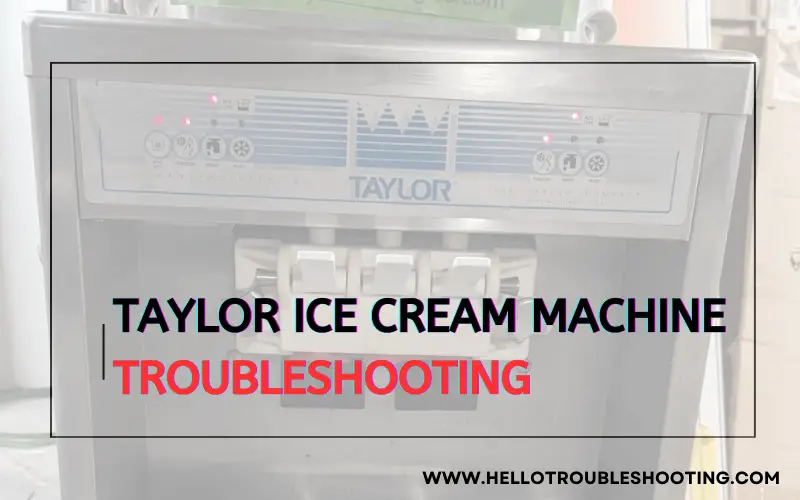
Common Issues
Running a Taylor ice cream machine can be rewarding but sometimes, issues arise. Understanding common problems helps in quick troubleshooting. Below are frequent issues with Taylor ice cream machines and their solutions.
Machine Not Freezing
If your Taylor ice cream machine is not freezing, it can be frustrating. Here are some common causes and solutions:
Issue | Possible Causes | Solutions |
---|---|---|
Power Issues | Power cord unplugged or faulty | Ensure the power cord is properly plugged in. Check for any damage. |
Thermostat Settings | Incorrect thermostat settings | Adjust the thermostat to the correct setting for freezing. |
Refrigerant Levels | Low refrigerant levels | Check refrigerant levels. Refill if needed. Consult a technician. |
Inconsistent Texture
Inconsistent texture in your ice cream can be a sign of several issues. Consider these potential causes and solutions:
- Improper Mixing:
Ensure ingredients are mixed evenly before adding to the machine.
- Incorrect Settings:
Check that the machine settings match the type of ice cream you are making.
- Dirty Machine:
Regularly clean the machine. Residue can affect texture.
Regular maintenance and understanding these common issues can keep your Taylor ice cream machine running smoothly.
Diagnosing Problems
Diagnosing problems with your Taylor ice cream machine can save you time and money. Understanding the issues helps you fix them faster. Let’s dive into two main methods: error codes and visual inspection.
Error Codes
Your Taylor ice cream machine shows error codes on its display. These codes help identify problems quickly. Refer to the machine’s manual for a list of common codes. Here are a few examples:
Error Code | Description |
---|---|
E1 | High Temperature |
E2 | Low Temperature |
E3 | Mix Out |
When you see an error code, consult the manual. It guides you through the steps to resolve the issue. Keep a list of common error codes handy for quick reference.
Visual Inspection
Performing a visual inspection is crucial. Look for signs of wear and tear. Check these areas:
- Hoses – Ensure they are not cracked or leaking.
- O-rings – Make sure they are not worn out.
- Mix hopper – Check for any residue or blockages.
Regularly inspect the machine’s exterior. Clean any visible dirt or debris. Examine the machine’s electrical components. Look for loose wires or connections.
These steps help maintain your machine’s efficiency. Regular inspections prevent minor issues from becoming major problems.
Cleaning And Maintenance
Proper cleaning and maintenance of your Taylor ice cream machine is crucial for its longevity and performance. This ensures the machine runs smoothly and produces high-quality ice cream. Below are some essential tips on daily cleaning routines and deep cleaning practices.
Daily Cleaning Routine
A daily cleaning routine is essential for maintaining hygiene and machine efficiency. Here’s a simple guide:
- Turn off the machine and disconnect it from the power source.
- Remove all removable parts such as the hopper, blades, and any other detachable components.
- Wash the parts with warm, soapy water. Rinse thoroughly to remove all soap residues.
- Use a clean cloth to wipe the exterior of the machine. Focus on areas that come into direct contact with ice cream.
- Reassemble all parts and ensure they are dry before reconnecting the machine to the power source.
Performing these steps daily helps in preventing any build-up of residue, which could affect the taste and quality of your ice cream.
Deep Cleaning Tips
Deep cleaning should be done weekly or bi-weekly, depending on the machine’s usage. Follow these tips for an effective deep clean:
- Disassemble the machine completely, including the internal components.
- Soak all parts in a sanitizing solution for at least 15 minutes. This helps in killing any bacteria that regular cleaning might miss.
- Scrub each part with a soft brush to remove any stubborn residues or buildups.
- Clean the machine’s interior with a food-safe sanitizer. Ensure you reach all corners and crevices.
- Rinse all parts thoroughly and let them air dry before reassembling the machine.
Regular deep cleaning ensures that your Taylor ice cream machine remains in top condition, providing consistent and delicious ice cream.

Credit: www.taylorwi.net
Electrical Issues
Electrical issues can be frustrating with Taylor Ice Cream Machines. They can stop production and cause delays. Understanding common electrical problems helps with quick fixes. This section covers two key areas: Power Supply Check and Circuit Breaker Reset. These checks can resolve many issues.
Power Supply Check
The first step is to check the power supply. Ensure the machine is plugged in securely. Look at the power cord for any visible damage. If the cord is damaged, replace it immediately.
Next, check the outlet. Use a tester to see if the outlet is working. If the outlet is not providing power, try another outlet. Ensure the outlet matches the machine’s voltage requirements.
Circuit Breaker Reset
Sometimes, the problem lies with the circuit breaker. Locate your main electrical panel. Find the breaker that controls the ice cream machine. It might be labeled for easy identification.
If the breaker is tripped, switch it off first. Wait a few seconds, then switch it back on. This can reset the power supply to the machine. If the breaker trips again, there may be a larger issue. Consider consulting an electrician.
Electrical Issues Table:
Issue | Solution |
---|---|
Machine not turning on | Check power supply and outlet |
Breaker tripping frequently | Reset breaker or consult electrician |
Power cord damage | Replace power cord |
Mechanical Failures
Mechanical failures in your Taylor ice cream machine can halt your business. Knowing how to troubleshoot these issues is vital. Let’s explore some common mechanical failures and how to fix them.
Motor Problems
The motor is the heart of your Taylor ice cream machine. Motor problems can lead to the machine not working at all. Here are some common motor issues:
- Overheating: A motor can overheat if it’s overworked or not well-ventilated.
- Unusual Noises: Grinding or whining noises usually indicate a problem inside the motor.
- Failure to Start: This can be due to a faulty power supply or a broken motor.
To fix these issues:
- Check for any obstructions blocking the motor’s ventilation.
- Ensure the machine is not running for too long without breaks.
- Inspect the power supply and ensure it is stable.
- If needed, consult with a professional for motor repairs.
Gear Issues
Gear issues can affect the machine’s ability to churn ice cream. Gears can wear out or break over time. Here are some signs of gear problems:
- Grinding Noises: This could indicate worn-out gears.
- Ice Cream Consistency: Poor consistency can be due to gear problems.
- Machine Stops: If the machine stops unexpectedly, a gear might be broken.
To troubleshoot gear issues:
- Inspect the gears for any signs of wear and tear.
- Lubricate the gears to ensure smooth operation.
- Replace any broken or worn-out gears.
- Regularly maintain the gears to prevent future problems.
Addressing these mechanical failures promptly can keep your Taylor ice cream machine running smoothly. Regular maintenance is key. Always consult the user manual or a professional if you’re unsure.
Part Replacements
Maintaining your Taylor ice cream machine is crucial for its performance. Part replacements are often necessary to keep it running smoothly. This guide helps you identify worn parts and source new ones efficiently.
Identifying Worn Parts
Regular inspections prevent larger issues. Look for signs of wear and tear. Common parts that may need replacing include:
- Blades – Check for dull or chipped edges.
- Seals – Inspect for cracks or leaks.
- O-rings – Look for signs of stretching or wear.
Use a flashlight to spot small damages. Listen for unusual noises. If the machine vibrates more than usual, it may indicate a worn part.
Sourcing New Parts
Finding the right parts is essential. Always use genuine Taylor parts. They ensure compatibility and longevity. Here are a few ways to source new parts:
- Manufacturer’s website – Directly order from Taylor’s official site.
- Authorized dealers – Purchase from certified sellers.
- Local suppliers – Check with local vendors for availability.
Keep the model number of your machine handy. It helps in finding the exact parts you need. Verify the part numbers before purchase. This ensures you get the correct replacements.
Consider keeping a small inventory of common parts. It reduces downtime during peak hours. Regular maintenance and timely replacements keep your machine efficient.
Professional Assistance
Sometimes, Taylor ice cream machines may face issues beyond basic troubleshooting. In such cases, professional help is crucial. Knowing when to seek expert assistance can save time and prevent further damage.
When To Call A Technician
There are several signs that indicate it’s time to call a technician for your Taylor ice cream machine. Here are a few common scenarios:
- Frequent Breakdowns: If your machine breaks down often, a technician’s expertise is needed.
- Unusual Noises: Strange sounds might point to internal issues that require professional care.
- Inconsistent Ice Cream Quality: If the texture or taste is off, a technician can diagnose and fix the problem.
- Electrical Problems: Issues with the machine’s power supply or wiring are best handled by an expert.
Calling a technician promptly can prevent small issues from becoming major problems.
Finding Reliable Service
Locating a trustworthy service provider is essential. Here’s a guide to help you find reliable service:
Step | Action |
---|---|
1 | Check online reviews and ratings. |
2 | Ask for recommendations from other business owners. |
3 | Ensure the technician is certified to work on Taylor machines. |
4 | Compare service rates to get a fair price. |
Taking these steps will help you find a reliable technician who can keep your machine running smoothly.
Preventative Measures
Preventative measures are essential for keeping your Taylor ice cream machine in top shape. Simple steps can prevent costly repairs and downtime. In this section, we’ll discuss key preventative measures.
Regular Inspections
Regular inspections help catch problems early. Check the machine weekly for any signs of wear or damage. Look for leaks, unusual noises, and temperature fluctuations. Early detection can save you time and money.
Component | Inspection Frequency | Signs of Wear |
---|---|---|
Hopper | Weekly | Cracks, leaks |
Beater Blades | Weekly | Wear, chipping |
Drive Belt | Monthly | Fraying, slack |
Gaskets | Monthly | Cracks, stiffness |
Scheduled Maintenance
Scheduled maintenance keeps the machine running smoothly. Follow the manufacturer’s guidelines for servicing. Regular servicing can extend the life of your machine. Key tasks include:
- Lubricating moving parts
- Replacing worn-out components
- Cleaning internal mechanisms
- Checking electrical connections
Keep a maintenance log. Record all services and repairs. This helps track the machine’s condition. It also aids in future troubleshooting.
By following these preventative measures, you can ensure your Taylor ice cream machine performs at its best.
Frequently Asked Questions
Why Is My Taylor Ice Cream Machine Not Freezing?
Your Taylor ice cream machine might not be freezing due to low refrigerant levels. Check the compressor and ensure it’s functioning properly. Also, inspect for any blockages in the freezing cylinder.
How Do I Reset My Taylor Ice Cream Machine?
To reset your Taylor ice cream machine, press the reset button located on the control panel. Hold it for a few seconds. This action should reset the machine to its default settings.
What Causes My Taylor Machine To Leak?
Leaking in a Taylor ice cream machine can be caused by worn-out seals or gaskets. Inspect these parts for damage. Replace them if necessary to prevent further leaks.
Why Is My Taylor Machine Making Loud Noises?
Loud noises in a Taylor ice cream machine may indicate a mechanical issue. Check the motor and drive belt for wear and tear. Lubricate moving parts if needed.
Conclusion
Troubleshooting your Taylor Ice Cream Machine can be simple. Follow the steps outlined. Ensure regular maintenance for smooth operations. Address issues promptly to avoid downtime. Keep your machine clean and parts in good condition. This will ensure a longer life for your equipment.
Happy ice cream making!