To troubleshoot a Liftmaster gate opener, check the power source and ensure the remote batteries are functional. Verify that the sensors are clean and aligned.
Liftmaster gate openers offer convenience and security, but like all devices, they can encounter issues. Common problems include power interruptions, remote control malfunctions, and sensor misalignment. Regular maintenance and basic troubleshooting can solve many of these issues. Begin by checking the power source and remote batteries.
Then, ensure that the safety sensors are clean and properly aligned. If problems persist, consult the manual or contact customer support. Proper troubleshooting can extend the life of your gate opener and ensure reliable operation. Understanding these basic steps can save time and reduce frustration.
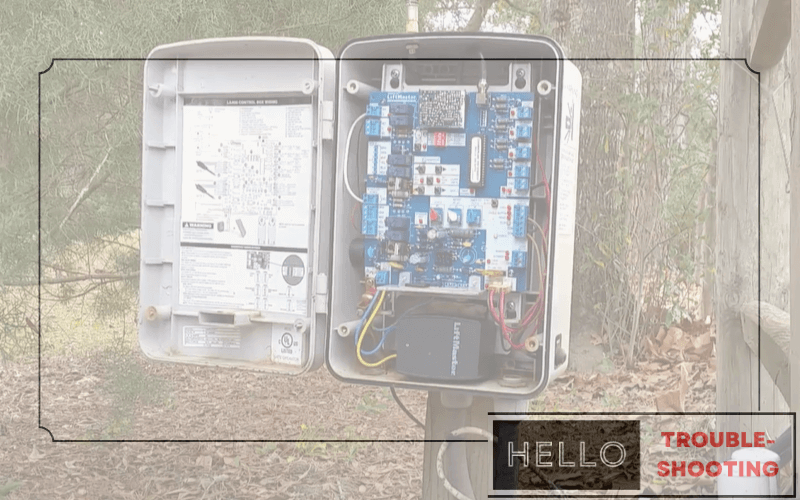
Common Issues
Liftmaster gate openers are reliable and efficient. But sometimes, issues arise. This section covers common problems and their solutions.
Gate Not Opening
Is your Liftmaster gate not opening? This can be frustrating. Here are some common causes:
- Power supply issues: Check if the gate opener has power.
- Remote control problems: Ensure the remote has working batteries.
- Obstructions: Make sure nothing is blocking the gate’s path.
Let’s dive deeper into each cause:
Cause | Solution |
Power Supply | Check the main power source. Ensure the outlet works. |
Remote Control | Replace batteries. Reprogram the remote if needed. |
Obstructions | Clear any objects blocking the gate’s path. |
Gate Stuck Midway
Is your gate getting stuck halfway? This is a common issue. Here are some possible reasons:
- Track obstructions: Debris or objects on the track.
- Mechanical issues: Worn-out gears or chains.
- Sensor problems: Misaligned or dirty sensors.
Here’s a closer look at these reasons:
- Track obstructions: Inspect the track. Remove any debris.
- Mechanical issues: Check gears and chains. Replace if worn.
- Sensor problems: Clean sensors. Ensure they are aligned.
These steps can help resolve the issue quickly.
Basic Checks
When your Liftmaster gate opener isn’t working, start with the basics. Basic checks often solve many issues quickly. Below are the essential checks to perform first.
Power Supply
Ensure the gate opener has power. A tripped breaker or blown fuse can cut power. Check the breaker box and reset if needed. Verify the power cord is plugged in securely. Look for any visible signs of damage on the power cord.
Check | Action |
Breaker Box | Reset the breaker |
Power Cord | Inspect for damage |
Outlet | Ensure it’s functional |
Remote Batteries
Remote batteries can die and need replacement. Open the remote’s battery compartment. Remove the old batteries and insert new ones. Make sure the batteries are placed correctly. Test the remote after replacing the batteries.
- Open the battery compartment
- Remove old batteries
- Insert new batteries
- Check battery placement
- Test the remote
Basic checks are crucial for troubleshooting your Liftmaster gate opener. Ensuring power supply and fresh remote batteries can often solve the problem.
Sensor Problems
Liftmaster gate openers rely on sensors to function correctly. These sensors ensure safe operation by detecting obstacles. Sensor problems can cause the gate to malfunction, posing safety risks.
Misaligned Sensors
Misaligned sensors are a common issue in gate openers. If the sensors are not aligned, the gate won’t close properly. To check for misalignment, inspect the sensors on both sides of the gate. They should face each other directly. Use a measuring tape to ensure they are at the same height.
Here’s a simple table to help you troubleshoot misaligned sensors:
Step | Action |
1 | Turn off the gate opener. |
2 | Check the sensor brackets for bends. |
3 | Realign the sensors until they face each other. |
4 | Turn the gate opener back on and test. |
Dirty Sensors
Dirty sensors can also cause issues. Dust, dirt, and cobwebs can block the sensor’s view. This interference can prevent the gate from closing. Regular cleaning helps keep sensors in good working condition.
Follow these steps to clean dirty sensors:
- Turn off the gate opener.
- Use a soft cloth to wipe the sensor lenses.
- Check for any spider webs or debris around the sensor area.
- Turn the gate opener back on and test the gate.
Keeping sensors clean ensures smooth gate operation. Regular maintenance can prevent many common problems.
Mechanical Issues
Mechanical issues with a Liftmaster gate opener can disrupt its operation. Common problems include obstructions and worn-out parts. Addressing these issues ensures smooth and safe gate functionality.
Obstructions
Obstructions can stop your Liftmaster gate opener from working correctly. Check for any debris or items blocking the gate’s path. Clear away leaves, sticks, or any objects around the gate.
Inspect the gate’s track for any foreign objects. Even small items can cause big problems. Make sure the track is clean and clear. This ensures the gate moves smoothly.
Look for plants or bushes that might be in the way. Trim back any overgrowth to ensure the gate has a clear path. Regular maintenance prevents these obstructions from causing issues.
Worn Out Parts
Over time, parts of your Liftmaster gate opener can wear out. Check the rollers for signs of wear and tear. Worn rollers can cause the gate to move unevenly or stop working.
Inspect the hinges of the gate. Rusty or loose hinges can affect the gate’s movement. Tighten loose hinges and replace rusty ones to ensure smooth operation.
The drive belt or chain can also wear out. Look for cracks or signs of wear. Replace the belt or chain if necessary. A new belt or chain can make a big difference.
Use the table below to keep track of parts that may need replacement:
Part | Signs of Wear | Action |
Rollers | Uneven movement, noise | Replace |
Hinges | Rust, looseness | Tighten or replace |
Drive Belt/Chain | Cracks, wear | Replace |
Motor Malfunctions
Motor malfunctions in your Liftmaster gate opener can cause major issues. These problems can disrupt the smooth operation of your gate. In this section, we will focus on common motor issues like overheating and strange noises.
Overheating
Motor overheating is a common problem. It can occur due to several reasons. Here are some potential causes and solutions:
- Continuous Use: Using the gate opener repeatedly without breaks can overheat the motor. Let the motor cool down for a while.
- Blocked Ventilation: Ensure the motor’s ventilation is clear. Remove any debris or dirt blocking it.
- Old Motor: An aging motor can overheat more frequently. Consider replacing it if it is too old.
Strange Noises
Strange noises from your gate opener indicate potential issues. Identifying these sounds can help diagnose the problem. Here are some common noises and their causes:
Noise Type | Possible Cause | Solution |
Grinding | Worn-out gears | Inspect and replace gears |
Clicking | Obstruction in the track | Remove any blockages |
Banging | Loose components | Tighten all bolts and screws |
Regular maintenance can prevent these issues. Keep your gate opener running smoothly.
Programming Errors
Programming errors can hinder your Liftmaster gate opener’s functionality. These errors often arise from incorrect settings or outdated codes. This section explains how to resolve these programming issues effectively.
Resetting The System
Resetting your Liftmaster gate opener can fix many problems. Follow these steps to reset your system:
- Locate the “Learn” button on your opener.
- Press and hold the “Learn” button for 10 seconds.
- Release the button when the LED light turns off.
- Your system is now reset and ready for new programming.
This reset clears all previous settings and codes. It gives you a fresh start for programming.
Reprogramming Remotes
After resetting, you need to reprogram your remotes. Here’s how to do it:
- Press the “Learn” button on your opener.
- The LED light will turn on for 30 seconds.
- Within this time, press the button on your remote.
- The LED light will blink, indicating successful programming.
Repeat these steps for each remote you use. Always test your remotes after programming to ensure they work correctly.
Reprogramming ensures your system recognizes new codes. This step is crucial for secure and efficient operation.
Weather Effects
Weather can significantly affect the performance of your Liftmaster gate opener. Different weather conditions pose unique challenges. Understanding these weather-related issues can help you keep your gate opener functioning smoothly.
Cold Weather Issues
Cold weather can cause your gate opener to malfunction. The freezing temperatures can make the metal parts contract. This may lead to misalignment and operational issues.
- Battery Problems: Cold weather can drain the battery faster.
- Lubrication: Grease can thicken, causing the gate to move slowly.
- Ice Accumulation: Ice can form on the tracks, obstructing movement.
Rain And Moisture Problems
Rain and moisture can cause significant issues with your gate opener. Water can seep into electrical components, causing short circuits.
- Electrical Short Circuits: Water can cause the system to fail.
- Rust: Moisture can lead to rust, weakening the gate.
- Sensor Issues: Moisture can fog up sensors, affecting their efficiency.
To mitigate these issues, you can take some preventive measures. For cold weather, ensure regular maintenance and use weather-resistant lubricants. For rain and moisture, ensure all electrical components are sealed and covered. Regularly check and clean the sensors to keep them functioning properly.
Maintenance Tips
Regular maintenance of your Liftmaster Gate Opener ensures it runs smoothly. Following some basic tips can help you avoid costly repairs. Below, we provide crucial maintenance tips to keep your gate opener in top shape.
Regular Lubrication
Lubrication is vital for the longevity of your gate opener. Use a silicone-based lubricant to grease moving parts. Avoid using oil-based lubricants as they attract dust and grime.
- Lubricate the chain or screw drive every six months.
- Apply lubricant to the hinges and rollers.
- Ensure even coverage for all moving parts.
Proper lubrication reduces friction and wear. It keeps your gate running smoothly. Always follow the manufacturer’s guidelines for the best results.
Routine Inspections
Regular inspections help identify potential issues early. Conduct a thorough check every three months.
- Inspect the gate for visible damage or rust.
- Check the electrical connections for any signs of wear.
- Ensure the safety sensors are clean and aligned.
If you notice any issues, address them immediately. Regular inspections can prevent bigger problems down the line. Always keep a checklist to ensure nothing is overlooked.
Common Maintenance Tools
Tool | Purpose |
Silicone-based Lubricant | Lubricates moving parts |
Wrench Set | Tightens loose bolts |
Multimeter | Checks electrical connections |
Cloth | Cleans sensors and other parts |
Having the right tools makes maintenance easier and more effective.
Frequently Asked Questions
How Do I Reset My Liftmaster Gate Opener?
To reset, press and hold the “Learn” button until the LED turns off.
Why Is My Liftmaster Gate Opener Beeping?
A beeping sound usually indicates low battery or a system error.
What Causes Liftmaster Gate Opener To Stop Working?
Common issues include power outages, misaligned sensors, or dead remote batteries.
How Do I Program A Liftmaster Remote?
Press the “Learn” button, then press the remote button until the LED light blinks.
Why Is My Liftmaster Gate Opener Light Blinking?
Blinking lights often indicate sensor misalignment or an obstruction on the gate path.
Conclusion
Troubleshooting your Liftmaster gate opener can save time and money. Follow the steps outlined for effective solutions. Regular maintenance prevents future issues. Keep your gate operating smoothly with these tips. If problems persist, consider professional help. Enjoy reliable access and security with a well-maintained Liftmaster gate opener.