To troubleshoot a Viking gate operator, check the power supply and inspect the control board for any errors. Ensure all safety devices function properly.
Viking gate operators are renowned for their reliability and performance. Despite their durability, occasional issues may arise that require troubleshooting. Addressing problems promptly ensures the gate’s optimal functionality and safety. Common issues include power supply disruptions, control board malfunctions, and faulty safety devices.
Regular maintenance and timely repairs can prevent these problems. Always refer to the user manual for specific troubleshooting steps. Using the right tools and techniques can resolve most issues efficiently. For persistent problems, contacting a professional technician is advisable. Proper care extends the lifespan of your Viking gate operator, providing long-term security and convenience.
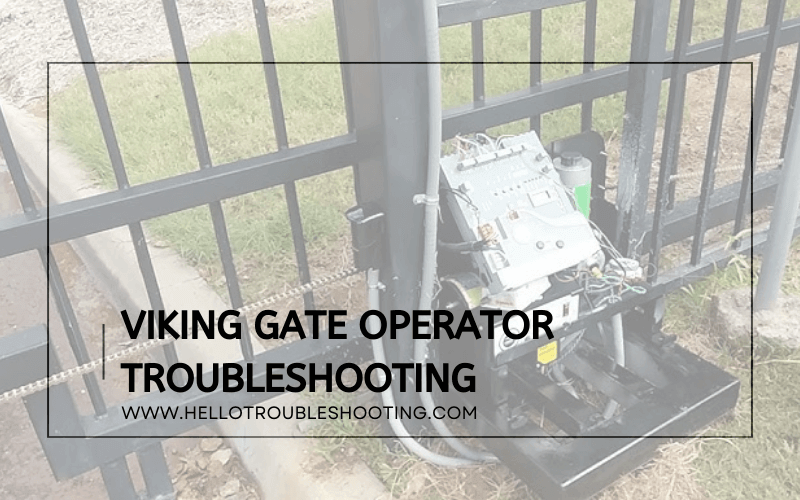
Common Issues
Viking gate operators are known for their reliability and efficiency. Yet, sometimes they encounter issues. Understanding common problems can save time and money. Below are some frequent troubles and how to handle them.
Gate Not Opening
If your Viking gate operator won’t open, check these possible causes:
- Power Supply: Ensure the gate operator is plugged in.
- Remote Control: Check the remote’s battery and signal range.
- Obstruction: Look for objects blocking the gate’s path.
- Manual Mode: Verify the operator is not in manual mode.
Follow these steps to diagnose:
- Inspect the power source for outages.
- Replace the remote control batteries if needed.
- Clear any debris or obstacles near the gate.
- Switch the operator back to automatic mode if it’s on manual.
Gate Stuck Midway
A gate stuck midway can be frustrating. Here are common reasons:
Problem | Solution |
---|---|
Debris in Track | Remove any dirt or objects in the track. |
Faulty Sensor | Check and clean the sensor lenses. |
Overheating | Let the motor cool down before retrying. |
Mechanical Issues | Inspect for broken parts and replace if needed. |
Check these steps to resolve the issue:
- Clear the track of any debris.
- Clean the sensors with a soft cloth.
- Allow the motor to rest if it’s overheated.
- Examine and replace any broken components.
Initial Diagnostics
Troubleshooting a Viking gate operator can seem daunting. Start with initial diagnostics to identify common issues. This helps in quickly pinpointing the problem and finding a solution.
Power Supply Check
First, ensure the gate operator has power. Without power, the gate won’t work. Follow these steps to check the power supply:
- Locate the power source.
- Verify the power switch is on.
- Check the circuit breaker. Reset if tripped.
- Inspect power cables for damage.
If the power supply is fine, move to the next step.
Remote Control Test
Next, test the remote control. A faulty remote can prevent the gate from opening or closing. Follow these steps to test the remote:
- Check the remote batteries. Replace if needed.
- Press the remote buttons. See if the gate responds.
- Stand closer to the gate. Sometimes, distance affects the signal.
- Reprogram the remote. Follow the manufacturer’s instructions.
If the remote works, the issue might be elsewhere.
Remember, these initial diagnostics are crucial. They help in identifying the root cause of the problem. Always start with the basics before diving into complex troubleshooting.
Mechanical Problems
Mechanical issues with your Viking gate operator can disrupt daily operations. Addressing these problems promptly ensures the gate functions smoothly. Below, we explore common mechanical problems and offer troubleshooting tips.
Hinge Inspection
Inspecting the hinges is crucial for maintaining gate functionality. Faulty hinges can cause the gate to misalign or jam. Follow these steps to inspect the hinges:
- Check for Rust: Rust can weaken the hinges.
- Look for Wear and Tear: Wear can affect gate movement.
- Lubricate the Hinges: Use a high-quality lubricant.
If you notice significant damage, replace the hinges promptly. Regular inspections can prevent bigger issues.
Track Alignment
Proper track alignment is essential for the smooth operation of sliding gates. Misaligned tracks can lead to grinding noises or complete failure. To check the alignment:
- Visual Inspection: Ensure the track is straight.
- Check for Obstructions: Remove any debris blocking the track.
- Measure the Distance: Use a measuring tape to check for consistent spacing.
If the track is misaligned, adjust it carefully. Consistent maintenance can help prevent track-related issues.
Electrical Failures
Electrical failures can be a major headache for Viking gate operators. These issues can cause the gate to malfunction or stop working entirely. It’s important to identify and address electrical problems promptly to ensure the gate operates smoothly. Below are some common electrical issues you may encounter.
Wiring Issues
Wiring issues are a common cause of electrical failures in Viking gate operators. Damaged or loose wires can disrupt the electrical flow, leading to operational problems. Here are some steps to troubleshoot wiring issues:
- Inspect all wires for visible damage or wear.
- Check for loose connections and tighten them if needed.
- Use a multimeter to test continuity of the wires.
If you find any damaged wires, replace them immediately. Properly securing all connections can also prevent future issues.
Circuit Board Problems
The circuit board is the brain of your Viking gate operator. If the circuit board malfunctions, the gate may not respond to commands. Follow these steps to troubleshoot circuit board problems:
- Power off the gate operator and remove the circuit board.
- Inspect the board for any burnt components or corrosion.
- Use a magnifying glass to check for cracked solder joints.
If you identify any damaged components, consider replacing the circuit board. Always consult the user manual or a professional technician for guidance.
Issue | Solution |
---|---|
Loose Wires | Tighten connections |
Damaged Wires | Replace wires |
Burnt Circuit Components | Replace circuit board |
By understanding and addressing these common electrical failures, you can keep your Viking gate operator running smoothly. Regular maintenance can also help prevent these issues.
Sensor Malfunctions
Viking gate operators rely on sensors to function correctly. These sensors ensure the gate operates safely and efficiently. Sensor malfunctions can disrupt this smooth operation. Understanding common issues helps in quick troubleshooting.
Obstruction Detection
Sensors detect obstacles in the gate’s path. If the sensor fails, the gate might not stop when an object is detected. This could cause damage or injury. Regularly check for debris around the sensor. Clean the sensor lens with a soft cloth.
Ensure the sensor is aligned properly. Misalignment can cause false readings. Make sure no objects block the sensor’s view. This includes plants, dirt, or other debris. Keep the sensor area clear for accurate detection.
Sensor Calibration
Proper calibration is crucial for sensor accuracy. An uncalibrated sensor can misread distances and objects. Follow the manufacturer’s instructions for calibration. This usually involves setting the sensor sensitivity.
Use a calibration tool if provided. Adjust the sensitivity to avoid false alarms. Too high sensitivity can cause unnecessary stops. Too low sensitivity may miss real obstacles. Regular calibration ensures the sensor works optimally.
Keep a log of calibration dates. Regular checks prevent long-term issues. Proper calibration ensures safety and efficiency of the gate operator.
Motor Troubles
Viking gate operators are reliable, but sometimes they face motor troubles. Addressing these issues ensures smooth operation and longevity. Let’s dive into common motor problems and their solutions.
Overheating Motor
An overheating motor can halt your gate’s operation. Overheating often indicates overuse or a faulty component.
- Check the motor for any debris or obstructions.
- Ensure the motor has proper ventilation.
- Inspect the thermal protection settings.
- Look for any worn-out parts that may need replacement.
Regular maintenance can prevent overheating. Clean the motor regularly and keep the area around it clear.
Motor Replacement
If the motor fails completely, replacement might be necessary. Follow these steps to replace a faulty motor:
- Disconnect the power supply to the gate operator.
- Remove the cover and locate the motor.
- Disconnect the motor from the control board.
- Unbolt the motor from its mounting bracket.
- Install the new motor and reconnect it to the control board.
- Secure the motor to the mounting bracket and replace the cover.
- Reconnect the power supply and test the gate operation.
Always follow the manufacturer’s guidelines for motor replacement. Safety first!
Maintenance Tips
Proper maintenance of your Viking gate operator ensures its longevity. Follow these tips to keep your gate operator in top shape.
Lubrication Advice
Lubrication is crucial for your gate operator. It reduces wear and tear. Use a high-quality lubricant for the moving parts. Apply it to hinges, chains, and gears. Avoid over-lubricating as it can attract dust and debris.
- Use high-quality lubricants
- Apply to hinges, chains, and gears
- Avoid over-lubrication
Regular Inspections
Regular inspections help identify issues early. Check for any signs of wear. Inspect the electrical connections for any damage. Ensure that the gate moves smoothly without any obstructions. Keep an eye out for unusual noises.
- Check for wear and tear
- Inspect electrical connections
- Ensure smooth gate movement
- Listen for unusual noises
Maintenance Task | Frequency |
---|---|
Lubricate moving parts | Every 6 months |
Inspect electrical connections | Every 3 months |
Check for wear | Monthly |
Professional Help
Troubleshooting your Viking gate operator can sometimes be tricky. Some issues need professional help. Knowing when to call a technician can save time and money. It ensures your gate operates safely and efficiently.
When To Call A Technician
Some gate issues require professional expertise. Here are signs you should call a technician:
- Gate not opening or closing: If your gate won’t move, call an expert.
- Strange noises: Unusual sounds can mean mechanical problems.
- Electrical issues: Flickering lights or power failures need a technician.
- Physical damage: Bent or broken parts require professional repair.
- Safety concerns: If safety features aren’t working, get help immediately.
Finding Reliable Services
Finding a trustworthy technician is crucial. Follow these tips to locate reliable services:
- Research online: Look for reviews and ratings of local services.
- Ask for recommendations: Friends and family can suggest reliable technicians.
- Check certifications: Ensure the technician is certified and insured.
- Get multiple quotes: Compare prices and services from different providers.
- Read the contract: Understand the terms and conditions before hiring.
Professional help is essential for complex gate issues. Knowing when to call a technician and finding reliable services can keep your Viking gate operator in top condition.
Frequently Asked Questions
Why Is My Viking Gate Not Opening?
Check the power supply and remote control batteries. Inspect the gate for obstructions and ensure the safety sensors are clean.
How To Reset Viking Gate Operator?
Locate the reset button on the control panel. Press and hold it for 10 seconds to reset the system.
What Causes Viking Gate To Stop Midway?
Possible causes include obstructions, low battery, or sensor issues. Check for physical barriers and ensure batteries are charged.
How To Troubleshoot Viking Gate Sensor Issues?
Clean the sensors with a soft cloth. Ensure they are aligned properly. Check for any visible damage or dirt accumulation.
Why Is My Viking Gate Making Noise?
Noise can be due to mechanical wear or debris in the tracks. Lubricate moving parts and clear any debris from the tracks.
Conclusion
Troubleshooting your Viking gate operator doesn’t have to be daunting. Follow these steps to ensure smooth operation. Regular maintenance can prevent common issues. Stay proactive and keep your gate functioning flawlessly. For persistent problems, professional help might be necessary. Keep your property secure and your gate reliable with these tips.